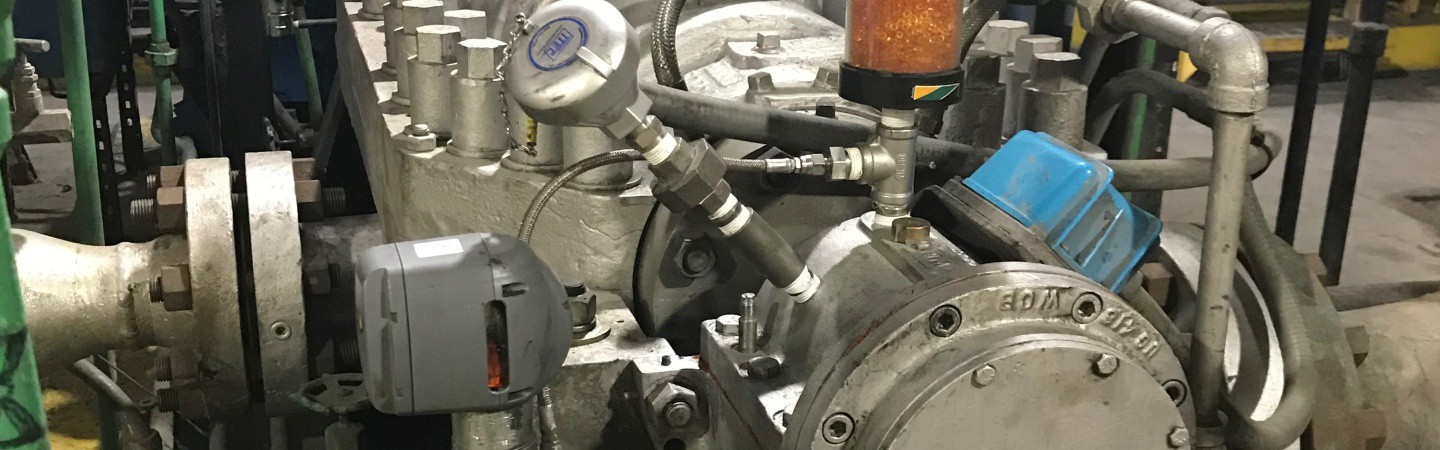
Dan Freeland
12.08.2020
Equipment lubrication protection is not a “one size fits all”
I recently looked at the analyst ratings of the tens of thousands of samples processed through our lab in 2020. I took all the samples related to bearings, gears, and hydraulic systems and summarized the analyst’s rating based on the test results. One thing is clear. Reliability and maintenance personnel continue to struggle with maintaining the quality of their lubricant. 35% of samples claim a Serious/Critical status, 27% proceed with caution, and only 38% are considered normal.
Equipment lubrication protection is not a “one size fits all” proposition. To equip your machines properly, to extend the working life of the lubricant, extend the mean time between oil changes, and ultimately equipment life, you need to assess each machine individually. You need to ask yourself what will make an impact on protecting the lubricant in each situation. What is required to protect both the quality and quantity of lubricant in that specific piece of equipment? Below we will look at 3 major categories of equipment/components and the best practices to manage the lubricant inside.
Pumps – Bearings
Bearings are the most common failure component in rotating equipment. Lubrication is often the culprit for that failure. A commonly referred to report by SKF tells us that 58% of bearing failures are attributed to insufficient lubrication and particle contamination. Again, referring to quality and quantity of the lubricant. Our data shows that 32% of the samples processed in 2020 on these applications are rated Critical (12.7%) or Serious (18.9%). Another 28.7% are Marginal.
There are thousands of these bearing applications that are related to process pumps, and the protection requirements are not the same either. A small cooling pump will not require the same protection as a boiler feed pump because criticality is a factor. The sump size could also be a factor in considering whether kidney loop filtration is applicable as opposed to top-offs or drain and refill. Critical Equipment that lubricates bearings with an oil bath should be equipped with the following as a minimum:
- Closed System Constant Level Lubricator – (Quantity and Quality) Failsafe way to ensure the oil is maintained at the proper level. Easy to check. Oil reserve to identify and account for small leaks or lubricant burn off. Closed to outside atmosphere. Shares bearing housing environment for pressure/vacuum conditions.
- Sampling Pitot Tube – (Quality) If your equipment is critical, you should be running periodic oil analysis to assure integrity of the oil chemistry. Pitot Tubes allows for consistent samples required for proper oil analysis.
- Level Indication – (Quantity) Either wireless or physical oil level monitoring.
- Desiccant Breather – (Quality) To manage the water ingression into the oil regardless of whether it is internally or externally generated. Eliminate particle contamination coming in from inferior vents and air filters.
- BS&W Bowl – (Quality) To identify free water in the sump.
Process pumps that are lower on the criticality scale may not require the BS&W bowl or Sampling Pitot Tube, as oil analysis may not be required. If the oil bath sump is sufficiently small enough, timed interval “drain and replace” lubricant procedures may suffice. However, Closed System Constant Level Lubricators (Quantity and Quality), Desiccant Breathers (Quality), and Viewports (Quantity) are still highly recommended.
Gears – Gearboxes
Ultimately, 54% of gearbox failures are a result of one of two things – Inadequate Lubrication (34.4%) and Contamination (19.6%). Yes again, over half of gearbox failures are attributed to quantity and quality of the lubricant. Our own oil analysis data suggests that almost 40% of the gearbox samples we processed this year were rated Critical (9.2%) or Serious (29.4%). If we would equate these samples to future failures, the total is better but not great. So how do we equip them to reduce failures? Gearboxes are unique in their ability to be mounted in different orientations, which can make a single universal solution difficult. Solutions are generally a kit of different parts specific to the application. This may entail a little more work on the front end but the life extension is worth it. Gearbox applications are best equipped with the following:
- Level Gauge: (Quantity) Easy to verify proper oil levels. Use a closed system level gauge to protect the integrity of the system.
- Desiccant Breathers: (Quality) Due to the amount of churning in a gearbox, there is typically an oil mist created inside the housing. Desiccant breathers may need to be mounted with a baffle or an elbow jog to reduce or eliminate mist entering the breather. Some breathers also have the expulsion ports at the bottom of the breather so mist is not able to enter the desiccant cartridge.
- Sampling Pitot Tube: (Quality) Critical gearboxes should be on an oil analysis program to monitor the quality of the lubricant. Ideally, these should be installed when the pitot tube length can be properly measured to assure the sample is taken from the “working zone” of the lubricant. If this is not an option, sampling ports are the next best option.
- Quick Connect Couplers: (Quality) Larger gearboxes with large lubricant reservoirs should include quick connect couplers for kidney loop filtration. Combined with regular oil analysis, filtration is an excellent way to clean your lubricant without shutting down the equipment. Doing filtration on a consistent schedule will significantly reduce particle contamination and impending failures.
Hydraulic Tanks for Hydraulic Systems
The hydraulic tank holds a quantity, sometimes very large quantity, of lubricant. This lubricant will typically move through a filter, and then pumped into precision components throughout the hydraulic system. It is important that the filter(s) in the system is selected with the proper ISO code levels in mind. These precision components can have requirements from 1-3 micron. It is therefore important we also keep the oil clean in the hydraulic tank before it even gets to the system filter.
It is widely reported that 70-80% hydraulic system failures are due to air and particle contamination. Most of which are courtesy of, of course, particle contamination. No surprise. As we look at the 2020 oil samples processed through Trico for hydraulic systems, again we are little better than that. 45.5% of samples processed were of the Serious/Critical variety, while 24.8% were Marginal and 29.7% were Normal. For the best oil analysis results in hydraulic tanks the following components are recommended:
Hydraulic Reservoir Kit: Hydraulic reservoirs are universally equipped with a breather cap like the one in the picture. Remove this cap and replace it with a multifunctional kit. This can include:
- Desiccant Breathers: (Quality) hydraulic tanks will breathe based on the intake and output of the pump and the system. These breathers are far superior to the vent cap. Also has a gauge to tell you if your breather is plugged.
- Sample Port and Pitot Tube: (Quality) To keep tabs on the quality, hydraulic tanks should be a part of an oil analysis program. This combination will provide repeatable oil samples to analyze.
- Quick Connect Couplers: (Quality) These couplers are important for kidney loop filtration. These tanks are often very large, so a dump and refill is not always cost effective. If your system has particle contamination, use portable filtration on a scheduled basis, or as recommended by oil analysis.
- Liquid Level Gauge: (Quantity) Provided a clear view of the tanks oil level. Use the closed system version to protect the system integrity.
- Portable Filtration: (Quality) Provides the necessary means to remove water and particulate in your hydraulic system. Remember to select your filters by the micron size required for your hydraulic system. Use in conjunction with the quick connect couplers and schedule a rotation for your tank and gearbox applications.
Proper Solutions
When comparing the industry failure data to the 2020 oil analysis data, it is evident that we need to continue to drive the importance of properly protecting lubricants inside equipment. This is done by setting up equipment with the proper solutions in the first place, focusing on the proper quantity and proper quality of the lubricant. If this can be achieved, lubricant life will be extended, mean time between oil changes will be extended, component life will be extended, and ultimately equipment life will be extended. This equates to dollars in the pocket and more time on the clock.
Protect Your Equipment
Need help with a solution recommendation? Contact us – we’ll be more than happy to help.
_______________________________________
**PRODUCT UPDATE 2/1/2024**- Trico is excited to share enhancements across our desiccant breather product line, now featuring both orange/green and blue/pink desiccant options. The EX-series breathers check valves are shielded, ensuring they remain free from clogs and stickiness upon exposure. Additionally, the Particulate Filter is 3-microns crafted from dual-phase micro-glass for superior filtration. The updated Watchdog Desiccant breathers have a versatile “tri-fit” connection, compatible with 1-inch or 3/8-inch male threads, adaptable for NPT, BSPT, or BSPP standards. Discover the new and improved Watchdog Desiccant Breathers today!