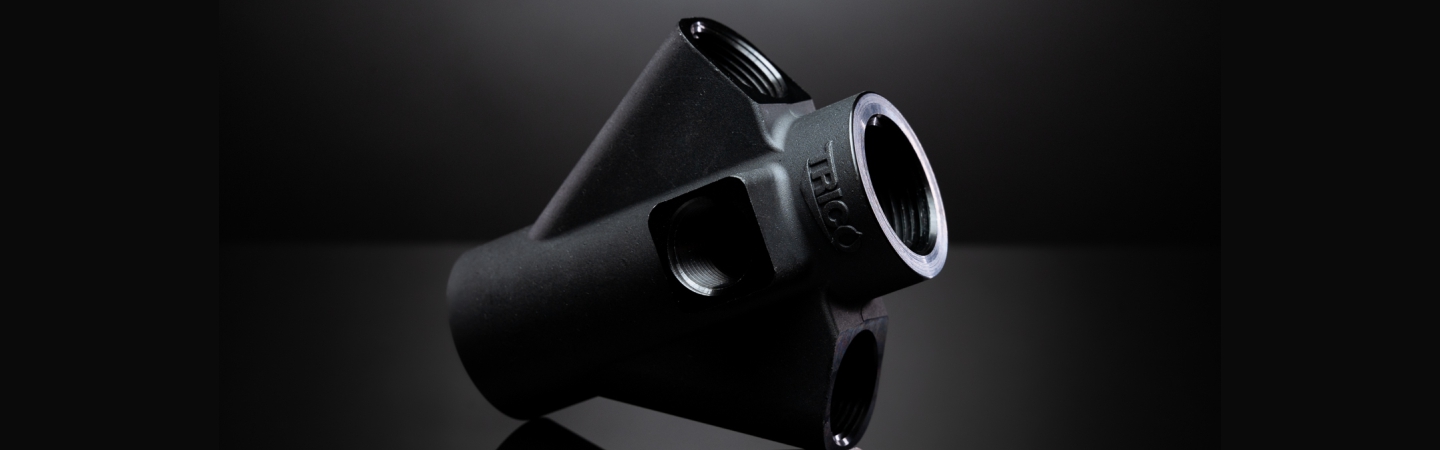
Dan Freeland
05.13.2025
Critical Access when Equipment Ports are Limited
Understanding Hydraulic Tank Contamination: Stats, Risks & Solutions
Contaminated hydraulic fluid is a silent system killer. Despite appearing clean, fluid can harbor hundreds of thousands of damaging particles that accelerate component wear and degrade performance. Recognizing contamination sources—and proactively addressing them—is vital for maintaining the health of your hydraulic system.
Contamination: The Root Cause of Most Failures
It’s widely acknowledged that 70% to 90% of hydraulic system failures are caused by contamination. This includes abrasive wear from particulates, water ingress, and chemical breakdown of the oil. Often these issues develop slowly—until valves stick, pumps grind, and downtime becomes unavoidable. Just because a tank looks sealed doesn't mean it’s protected. In many cases, inadequate access ports or outdated fittings prevent proper contamination control practices from being implemented.
Why Microscopic Contaminants Matter
Particles in the 6 to 14 micron range—too small to see—are the primary culprits behind hydraulic damage. These minute invaders scar precision surfaces and shorten component life significantly. Yet, they often go undetected until after a major failure.
ISO Cleanliness Standards: Why They Matter
The ISO 4406:1999 standard categorizes hydraulic fluid cleanliness using particle counts at ≥4μm, ≥6μm, and ≥14μm. Even brand-new oil can fall short of system requirements, especially in high-pressure environments. For example, an ISO 20/18/14 rating means:
- Nearly 1 million particles ≥4μm in just 100 ml of oil
- Over 130,000 particles ≥6μm
- Up to 8,000 particles ≥14μm
Overlooked Entry Points: Air Caps & Access Port Limitations
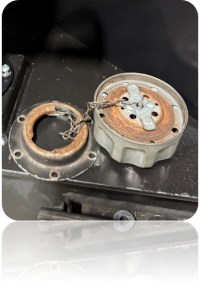
These outdated components:
- Corrode internally, flaking metal into your oil
- Lack any form of filtration or desiccation
- Provide poor sealing, allowing airborne debris and moisture inside
The Modern Approach: Equip Your Tank to Protect Your Oil
Today’s best practices go beyond simply filling and capping the reservoir. A fully equipped hydraulic tank should include:
- Quick Disconnects (top & bottom) for clean fluid transfer, fill operations, and closed-loop filtration (kidney-looping)
- Desiccant Breathers to prevent moisture and airborne debris from entering through venting
- Oil Sampling Devices like pitot tubes and dedicated sample ports for accurate time- or condition-based oil analysis
- Machine Vitals™ or similar sensors to monitor lubricant health and ambient environmental data in near real-time
- Liquid Level Gauges for ensuring proper reservoir levels and preventing cavitation
- Drain Valves for safe and clean oil removal during servicing
Trico’s Tri-Core Multi-Port Adapter: One Solution, Many Capabilities
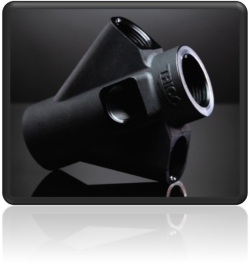
Key features include:
- Multiple NPT-threaded ports sized for real-world industrial needs
- Centralized access for breathers, sensors, sampling ports, quick connects, and more
- A compact, durable design that eliminates the need for modifying or welding new openings into the tank
- Ports Include: (2) Female 1” NPTs, (2) ¾” Female NPTs, (2) Female ½” NPTs
Final Word: Clean Oil Starts With Smart Design 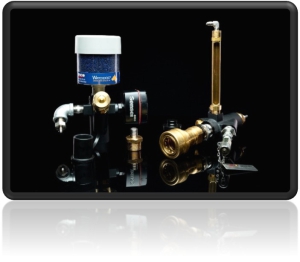
Hydraulic system reliability hinges on fluid cleanliness. But achieving that cleanliness isn’t just about filters—it starts with having the right infrastructure on your tank (or Gearbox) to support proactive maintenance, monitoring, and control. By upgrading old components like bayonet-style caps and installing Trico’s Tri-Core Adapter, you're not just able to properly protect your hydraulic oil, you're able to protect your entire system investment.
- Category:
- Application
- Contamination