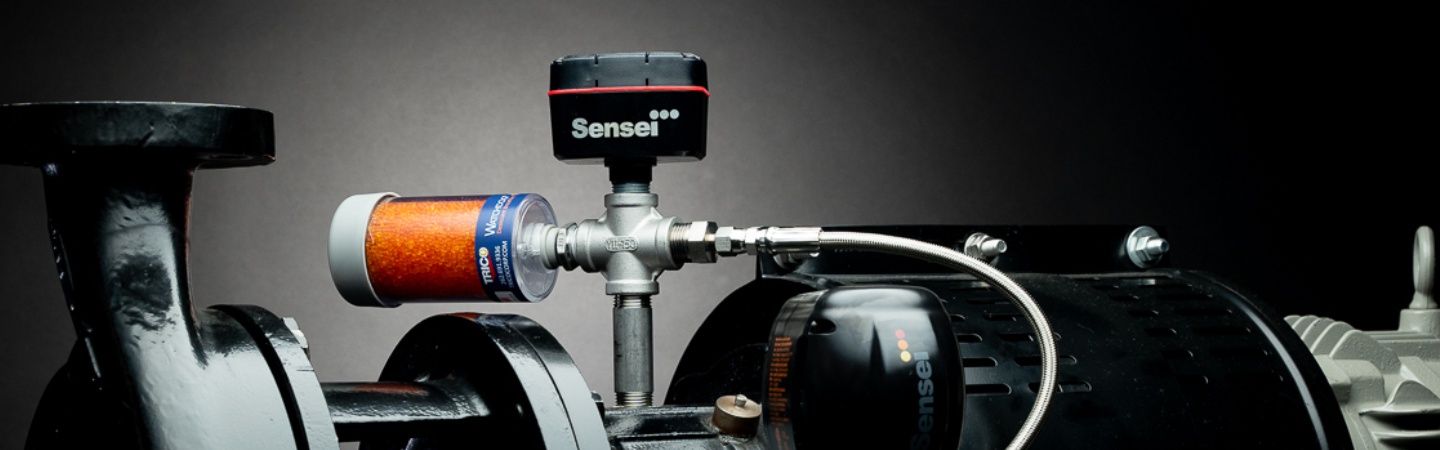
Lisa Kiepert
07.08.2025
The Invisible Enemy Inside Your Equipment
When most maintenance teams think about protecting machinery, their attention goes straight to the oil. They perform regular oil analysis, filter it to keep contaminants in check, and maintain a consistent level in the sump.
But there’s a critical area often overlooked: the air above the oil in oil lubricated equipment. It may seem harmless, but what happens in this small volume of air space can have a huge impact on the health of your lubricants and the life of your equipment.
What is Headspace Air?
Every gearbox, hydraulic reservoir, and similar piece of equipment contains an air pocket above the fluid level. This is known as “headspace” air.
It’s not static. As operating temperatures rise and fall, the oil and air expand and contract. When the system heats up, it pushes air out. As it cools, it draws air back in.
These repeated pressure changes effectively make your equipment “breathe,” constantly exchanging internal air with the outside environment. With each cycle, it pulls in whatever the surrounding atmosphere holds.
Why Pressure Changes in the Headspace Matter
Moisture Ingress
Warm air holds more water. When equipment breathes in humid air and then cools, moisture condenses on interior surfaces and often ends up in the oil. Even small amounts of water can shorten bearing life, accelerate wear and corrosion, and deplete additives, leading to reduced lubricant performance.
Dust and Particulate Contamination
Every intake of air is another opportunity to introduce microscopic contaminants. Silica, metal fines, and process dust can all get drawn inside. Once circulating in the oil, these particles increase abrasion and accelerate wear on gears, bearings, and other critical surfaces.
How to Protect Your Equipment
Use Desiccant Breathers
Installing desiccant breathers is an effective way to tackle headspace contamination. These devices remove moisture from incoming air and capture fine particles before they ever reach the oil. Keeping the headspace dry and clean directly minimizes many of the underlying causes of lubricant failure.
Go Further with Machine Vitals and Oil Analysis
While breathers provide essential frontline protection, adding condition monitoring sensors like Machine Vitals takes it a step further. These systems track internal pressure, humidity, and temperature in real time, helping you understand exactly how your equipment is breathing and whether it’s pulling in humid or contaminated air.
More importantly, Machine Vitals provides the bigger picture by showing how these conditions relate to one another over time, giving you a deeper understanding of what’s truly happening inside your equipment. Paired with oil analysis, it creates a comprehensive early-warning system that helps catch issues before they escalate.
A Practical Example
At one facility, simply replacing standard vent caps with desiccant breathers across multiple gearboxes reduced water content in the oil from over 1000 ppm to under 200 ppm. This straightforward change extended oil life, reduced bearing failures, and helped avoid major overhauls all by better managing what was happening in the headspace.
Don’t Overlook the Headspace
It’s easy to concentrate on what’s happening in the oil sump, but the air above your lubricant is just as critical. Pressure-driven breathing continually invites moisture and contaminants into your system. Paying attention to this often-ignored area is one of the smartest, easiest, most cost-effective steps you can take to strengthen equipment reliability and safeguard your lubrication investment. Contact us to learn how we can help you protect your headspace and keep your equipment running at its best.