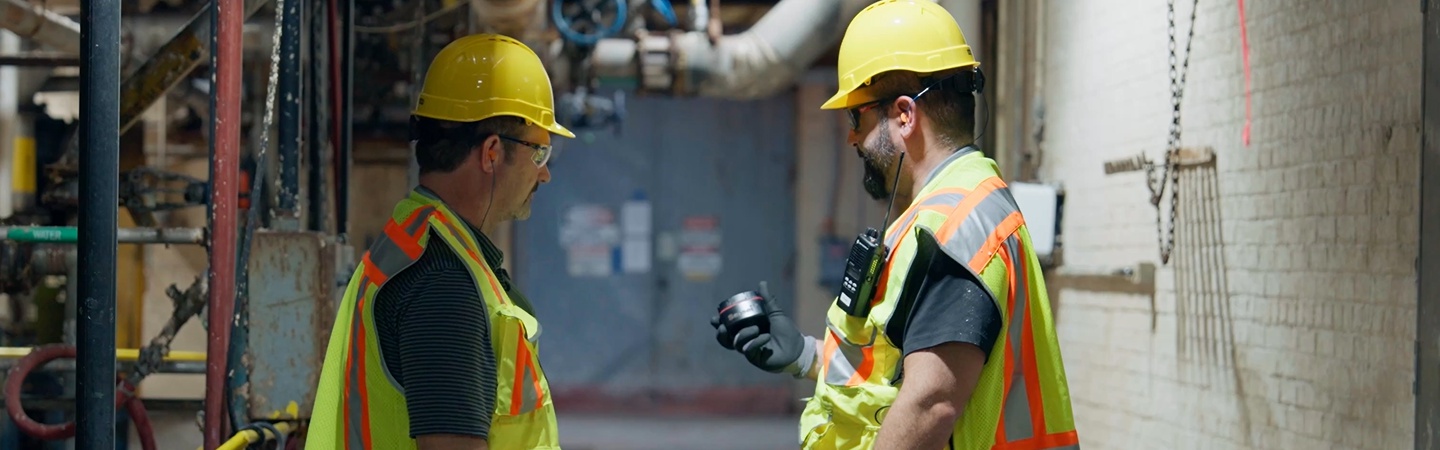
Dan Freeland
07.09.2024
Empowering Technicians, Managers, and Leaders with Smart Monitoring and Predictive Insights
In the bustling world of industrial maintenance, time is not just money; it's the lifeblood of operations. There is never enough of it, or enough qualified employees to get it done. Enter Machine Vitals, the innovative solution designed to make your life easier, whether you're on the shop floor or managing multiple sites. Let's take a look at how Machine Vitals can transform everyday tasks for various maintenance roles.
The Maintenance Technician: From Manual Checks to Smart Monitoring
Meet Joe, the Maintenance Technician.
Joe’s daily routine used to involve a lot of walking around and performing manual checks: oil levels, bearing temperatures, vibration analysis – you name it. Each of these tasks required specialized tools, careful measurement, countless steps, and meticulous recording.
What Joe Used to Do:
- Daily Oil Level Checks: Opening reservoirs, measuring, and topping up.
- Temperature Readings: Using handheld infrared thermometers to check for overheating.
- Vibration Analysis: Setting up sensors and interpreting complex graphs.
How Machine Vitals Helps:
- Automated Monitoring: With Machine Vitals installed, Joe gets real-time data on temperatures, humidity levels, vibrations, and audible trends sent directly to his tablet. No more manual measurements!
- Early Warnings: The device parameters alert Joe before minor issues become major problems, allowing for proactively planning maintenance events.
- Data Logging: Automated data logging means Joe can focus on fixing issues rather than documenting them. Joe can also record maintenance events via the app to keep a historical record of the equipment’s mechanical changes. These will be important for identifying what has changed and when in the event alarms are triggered.
The Maintenance Manager: From Firefighting to Strategic Planning
Meet Lisa, the Maintenance Manager.
Lisa used to spend her days putting out fires – literally and figuratively. Unplanned downtime, unexpected failures, and urgent repairs were all part of her daily grind. Finding the time and the personnel is always a futile battle.
What Lisa Used to Do:
- Daily Status Meetings: Long meetings to understand what went wrong and why.
- Scheduling Maintenance: Juggling team schedules to ensure coverage for emergency repairs.
- Equipment Inspections: Regular checks to anticipate potential issues.
How Machine Vitals Helps:
- Predictive Maintenance: With Machine Vitals' data, Lisa can predict when equipment will need maintenance, reducing unplanned downtime.
- Efficient Scheduling: Automated alerts and reports mean Lisa can plan maintenance activities around production schedules.
- Comprehensive Insights: Detailed reports provide Lisa with insights into equipment health, helping her make informed decisions and improve operational efficiency.
The District Manager: From Reactive Oversight to Proactive Management
Meet Mike, the District Manager.
Managing multiple sites, Mike's challenge was staying on top of maintenance needs across different locations, often dealing with problems after they had escalated.
What Mike Used to Do:
- Site Visits: Regular travel to each site to review maintenance logs and issues.
- Problem Solving: Addressing critical issues as they arose, often late and with incomplete information.
- Resource Allocation: Deciding where to allocate resources based on urgent needs.
How Machine Vitals Helps:
- Remote Monitoring: Mike can now monitor all his sites from a central dashboard, getting real-time updates on equipment status.
- Trend Analysis: Machine Vitals aggregates data across sites, helping Mike identify trends and address issues before they become critical.
- Optimized Resources: With a clear view of maintenance needs, Mike can allocate resources more effectively, reducing waste and improving response times.
The Corporate Maintenance Leader: From Data Silos to Data-Driven Decisions
Meet Louis, the Corporate Maintenance Division Leader.
Louis’s role involves overseeing the maintenance strategy for the entire corporation, a task complicated by questionable data sources and inconsistent reporting.
What Louis Used to Do:
- Monthly Reports: Gathering and analyzing maintenance reports from various sites, often with incomplete data.
- Strategy Development: Developing maintenance strategies based on historical data and best guesses.
- Budget Justifications: Justifying maintenance budgets with data that was often outdated by the time it was presented.
How Machine Vitals Helps:
- Unified Data Platform: Machine Vitals provides a single source of truth, aggregating data from all sites into one platform.
- Real-Time Analytics: Louis can access up-to-date analytics, making it easier to develop and adjust strategies based on current conditions.
- Informed Budgeting: With detailed, real-time data, Louis can make a compelling case for maintenance budgets, backed by hard facts.
Machine Vitals is more than just a sensor – it's a device that brings efficiency, reliability, and foresight to industrial maintenance. Whether you’re a hands-on technician like Joe, a strategic manager like Lisa, a district overseer like Mike, or a corporate leader like Louis, Machine Vitals simplifies your tasks, enhances your decision-making, and ultimately keeps your operations running smoothly.
Gone are the days of reactive maintenance and endless firefighting. With Machine Vitals, you're empowered to take control, anticipate problems, and keep your equipment – and your career – in peak condition. Embrace the future of maintenance today!