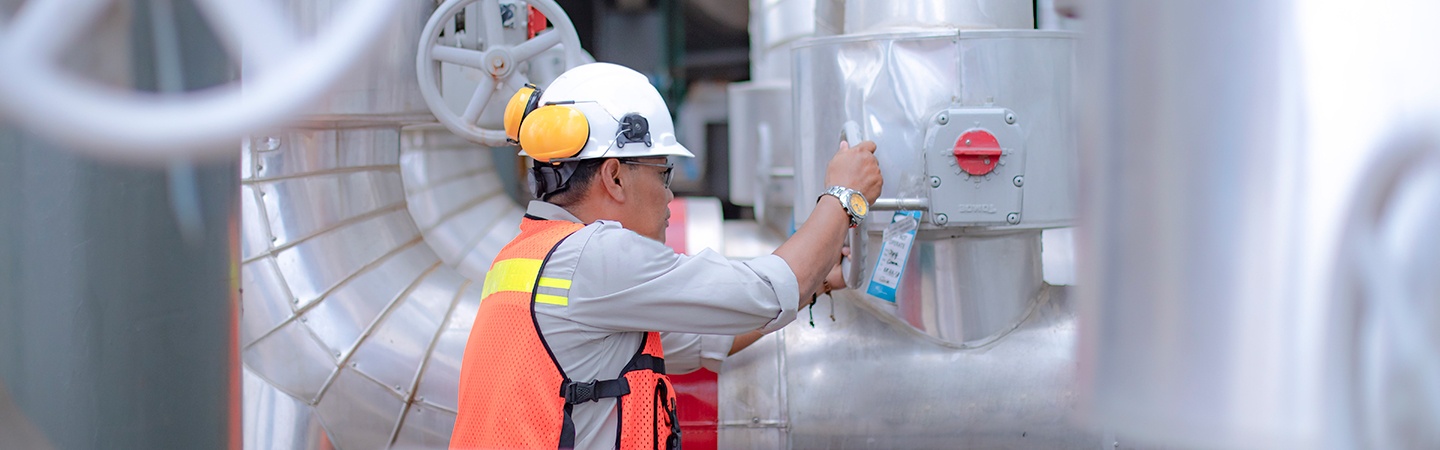
Jim Jung
02.12.2020
Transform Your Next Equipment Outage from a Necessary Evil into a Reliability Opportunity
The typical view of a scheduled plant shutdown is that it’s a chance to fix problems or perform routine maintenance.
That’s all well and good, but what if your next shutdown meant something more?
If your company is like many others, you’re probably struggling with labor shortages. In maintenance terms, that means a lot more firefighting and a lot less fire prevention – proactive, preventive activities.
With that context, a scheduled plant shutdown may be your best opportunity to catch up – and even get ahead. Your next outage is a great time to make changes that will allow you to better control and monitor what’s happening with your equipment.
Seizing this opportunity will take some forethought and planning. Most importantly, you should submit oil samples for analysis well in advance of your shutdown. (It especially helps to have good reference samples on file to compare against.) The insights from oil analysis can help you determine what needs to be done and what can and should wait.
Here’s a look at four key areas where you may be able to make a more lasting impact.
Oil Changes
If your typical shutdown includes equipment oil changes, it’s a good idea to question the need for these activities. They’re probably more costly than you think.
Trico recently published a calculator to better understand the true cost of these “routine” activities, so you might want to start there. As we pointed out in a recent post, extending the interval between oil changes can save your facility a lot of money.
For example, the largest refinery in Colombia had been changing the oil on 200 pumps in their plant every two weeks. But after completing some oil contamination-control upgrades, they’ve extended the interval to 6-8 months. That’s at least 12x as long as their previous oil change interval.
Your oil analysis results should be telling you which equipment is ready for a complete drain and refill and requires work orders as a part of the shutdown. If an oil change is required, you can also take this time to change equipment setups that will help you maximize uptime and reliability in the long run…
Visual Inspection
Visual inspection equipment at the machine is your first line of defense against emerging problems. Here’s more about what your team should be on the lookout for.
A shutdown is a good opportunity to upgrade with components such as:
- A 360 view inside a constant level oiler such as a Trico Opto-Matic
- A BS&W (bottom sediment and water) bowl / sump bottle
- A liquid level gauge with Pitot Tube
Filtration
Controlling water and particulate contamination in your oil is key to maintaining the reliability of your equipment.
If oil analysis shows contamination, filtration may be an option instead of simply changing the oil. During shutdown, you can add quick disconnects to your equipment, which allows you to pump the oil through a portable filtration cart while your equipment continues to run.
You’ll keep your equipment protected and, again, save money by increasing mean time between oil changes. As a bonus, using a filter cart to pump out oil can greatly expedite your next oil change vs. letting it drain – when it’s actually necessary, of course.
Oil Sampling
Acquiring consistent oil samples is crucial to getting accurate insight in oil analysis. Proper oil sampling equipment can help you ensure your whole team adheres to the same standard operating procedures.
Shutdown is a great time to eliminate the variability of sampling practices with drop tubes and drain sampling. Pitot tubes or sample ports can help standardize your process. These are both designed to collect samples under the equipment’s typical operating condition – another important factor.
Putting Multiple Upgrades Together
You might find it beneficial to combine multiple upgrades on a single piece of equipment. Here’s an example of how you’d upgrade a cooling tower gearbox. Or, here’s one for a new setup for a pump.
Not sure it’s worth the effort?
Most of these installations take no longer than a typical oil change. More importantly, the results are often dramatic, particularly in terms of lengthening the time between oil changes.
Don’t Miss Your Shutdown Opportunity
Trico can help you capitalize on your next shutdown to get ahead of the reliability game. Click below for additional recommendations as your shutdown approaches.
- Category:
- Oil Analysis