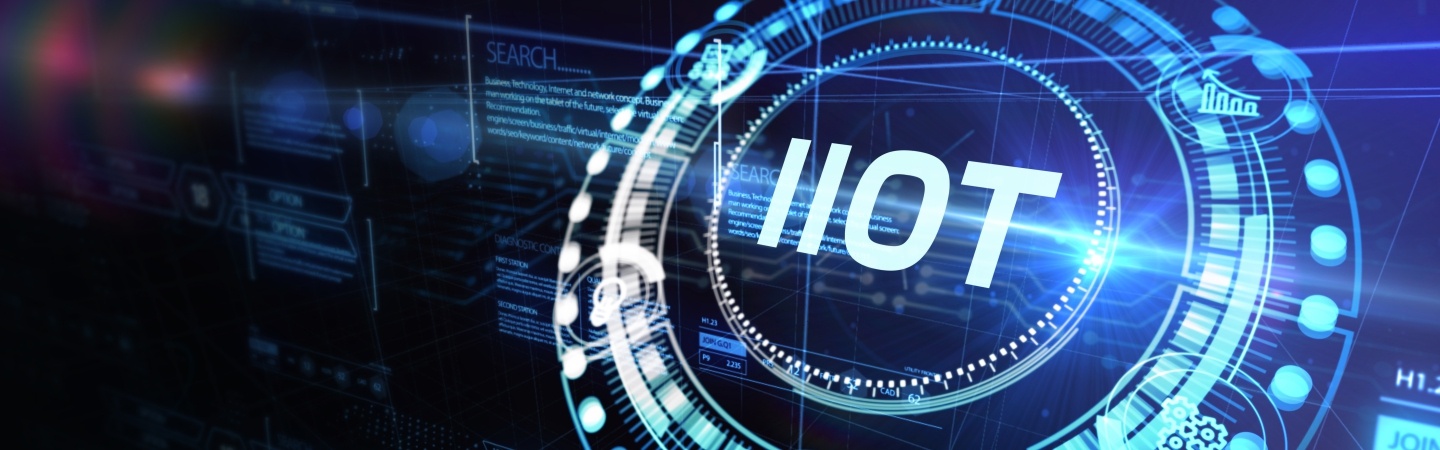
Dan Freeland
01.09.2024
Exploring the Advantages of IIoT and Overcoming Challenges in Industrial Maintenance
In the ever-evolving world of industrial maintenance, there has been a significant shift from traditional, time-consuming lubrication routes to leveraging the power of the Industrial Internet of Things (IIoT). This article explores the contrast between conventional lube routes and IIoT in maintenance activities and highlights the advantages of embracing the latest technologies in monitoring equipment. We will delve into the challenges faced by maintenance professionals, including the physical demands of walking around large manufacturing plants, labor shortages, and the transition from a retiring "tribal knowledge" workforce to a data-driven, internet-savvy generation.1. The Time-Consuming Nature of Conventional Lube Routes:
Maintaining equipment in a large manufacturing plant often involves physically walking to each piece to perform lubrication tasks. This method is not only time-consuming but also leaves room for human error. Furthermore, the repetitive nature of these routes can lead to inefficiencies, safety issues, and reduced productivity. With the increasing complexity and scale of industrial operations, a more efficient approach is needed to optimize maintenance activities.
2. Labor Shortages and the Retirement of Tribal Knowledge Workforce:
The industrial sector is facing a significant challenge with the retirement of experienced professionals possessing tribal knowledge. These skilled workers with years of hands-on experience have been responsible for maintaining equipment and keeping operations running smoothly. However, as they exit the workforce, there is a gap that needs to be filled by a new generation of maintenance professionals who have different skill sets and approaches.
3. IIoT: Transforming Maintenance Activities:
The emergence of IIoT has revolutionized maintenance activities by providing real-time data and remote monitoring capabilities. Connected sensors embedded in equipment can collect vital information about performance, temperature, vibrations, and lubrication needs. This data is then fed into advanced analytics systems, allowing maintenance professionals to move from reactive to proactive maintenance practices, predicting and preventing potential failures.
4. Advantages of IIoT in Maintenance Activities:
- Enhanced Efficiency: IIoT eliminates the need for time-consuming, physical lube routes, allowing maintenance professionals to focus on more critical tasks and optimize their productivity.
- Data-Driven Decision Making: The wealth of data collected through IIoT enables maintenance professionals to make informed decisions based on real-time insights, reducing downtime and improving overall equipment effectiveness.
- Predictive Maintenance: By leveraging advanced analytics and machine learning algorithms, IIoT can detect patterns and anomalies in equipment behavior, enabling early identification of issues and timely preventive actions.
- Remote Monitoring: IIoT empowers maintenance professionals to remotely monitor equipment health, allowing them to address maintenance needs promptly and efficiently, regardless of the physical location of the equipment.
As the industrial world continues to evolve, it is crucial for organizations to understand the benefits of IIoT and adapt to this new era of maintenance. By embracing these technologies, businesses can unlock unprecedented efficiency, reduce costs, and maximize equipment lifespan, ultimately leading to enhanced competitiveness in an ever-changing global marketplace.