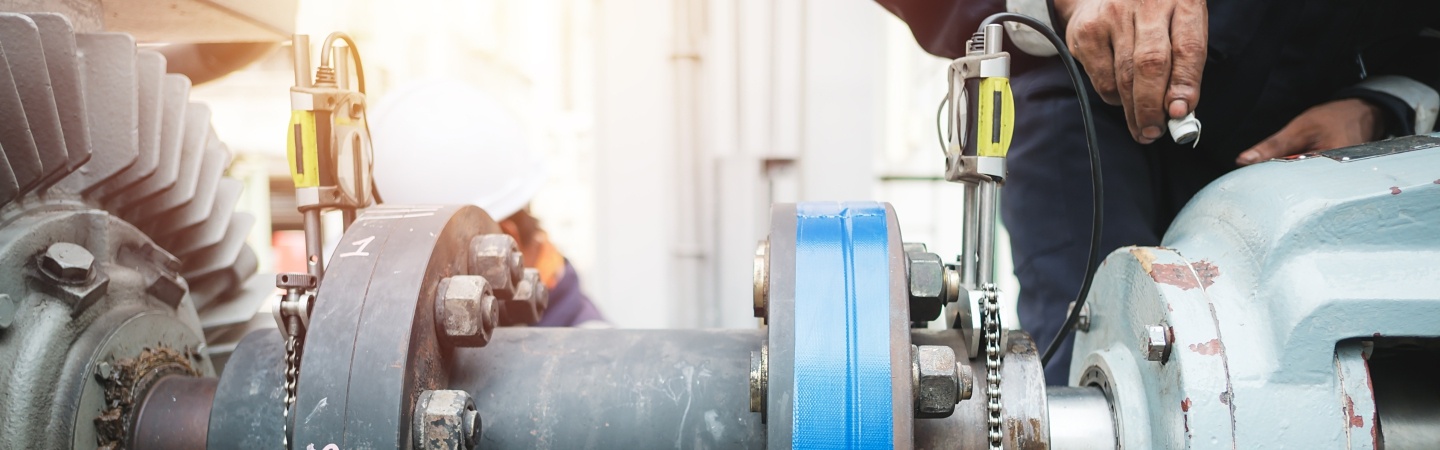
Dan Freeland
12.05.2023
Reduce Failures, Downtime, and Costs with Effective Strategies
Maintenance and reliability professionals let's get real for a minute. Rotating equipment is the backbone of any plant. Whether it's a motor, pump, agitator, or compressor, your operations are only as reliable as the equipment you rely on. As a maintenance or reliability professional, you're responsible for keeping this equipment in top working order. It's not always easy to do so, but by addressing these six issues, you could greatly reduce failures, downtime, and maintenance costs.
1. Poor Maintenance Practices:
Let's start with the most obvious one first. Poor maintenance practices are a major culprit of equipment failure. A survey was conducted which determined the majority of equipment problems were corrected much sooner if there existed a good maintenance program. But it's not just a matter of periodically checking equipment to see if it's still running. A good maintenance program needs to be properly implemented. Ensure the personnel conducting maintenance are properly trained, the necessary tools are always available, and the right parts inventory being maintained. A comprehensive maintenance program should establish a baseline from which you can detect when equipment is starting to deviate from normal operation. Consider adding wireless sensors that can track and set limits to these deviations. Address issues before they end up being major problems with unplanned outages.
2. Misalignment:
Misalignment could be a result of several factors such as wear and tear due to long-term use or incorrect installation. Misaligned equipment leads to a host of serious problems like excessive vibration, noise, and premature wear and tear on equipment components. Misalignment could also reduce the effectiveness and lifespan of equipment components, particularly when it comes to bearings. This means motor loads are significantly increased which often leads to motor failure or winding insulation issues.
3. Inadequate Lubrication:
Proper lubrication of rotating equipment is absolutely essential to their continued safe and efficient operation. Lack of lubrication could result in prematurely worn-out components, friction, and overheating issues. Correctly greasing equipment is crucial to keep the bearings and the moving parts working at optimal levels. Remember to frequently monitor lubrication needs, so your rotating equipment is properly lubricated all the time.
4. Temperature Fluctuations:
Whether devices are working under extreme heat or coldness, temperature fluctuations could dramatically affect the effectiveness or lifespan of machinery. This can lead to bearing damages, cracking, and leaks in pump casings. Proper steps should be taken to ensure that the temperature is always within the optimal range for each piece of equipment, depending on its design specifications.
5. Contamination:
Number one component killer. Contamination of the rotating equipment could be due to a number of things: dirt, dust, or moisture. We all have seen what happens to iron when it comes into touch with moisture. Frequent checks could be made to make sure that rotating machines are free from these contaminants which could cause additional friction, overheating, and eventually component and equipment failure.
6. Component Wear:
All rotating equipment has a lifespan, and they eventually wear out over time. When vital component wear occurs, it could lead to numerous problems in operations. Regular monitoring (Sensors) of equipment is critical in noticing and addressing wear and tear issues as they occur before they lead to more severe problems.
When it comes to ensuring the safety and efficiency of your plant equipment, attention to detail is vital to your success. By implementing an effective maintenance program, addressing misalignment, lubricating thoroughly, monitoring temperature fluctuations, avoiding contamination, and identifying component wear early on, you're certain to prevent equipment failure, reduce downtime, and lower maintenance costs. Online sensors have come a long way to aid in monitoring these situations.