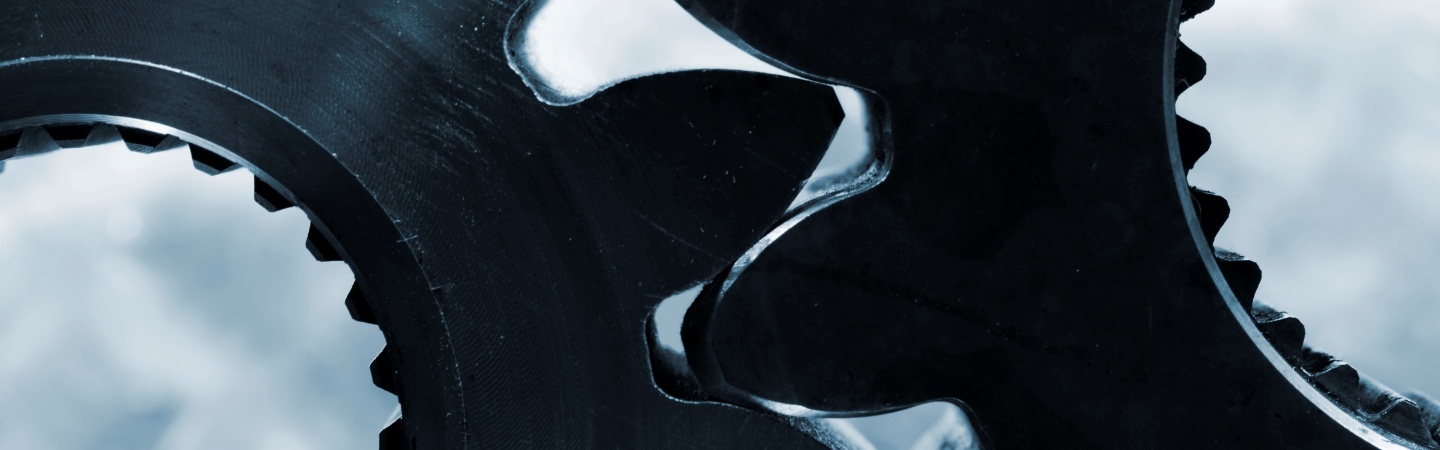
Dan Freeland
04.16.2024
Integrating Preventive and Predictive Maintenance to Enhance Equipment Health
In industrial maintenance, Condition Monitoring is a vital strategy for ensuring equipment reliability and efficiency. Central to this approach are Preventive maintenance and Predictive maintenance—two methodologies that, while distinct, are complementary in maintaining optimal machine operation. Understanding the nuances of each maintenance strategy not only enhances machine lifespan but also contributes significantly to a company's operational stability.What is Preventive Maintenance?
Preventive maintenance involves the periodic inspection and maintenance of equipment to lessen the likelihood of failures before they occur. This routine or scheduled maintenance is foundational in maintenance management systems and is widely deployed throughout the industry. The primary advantage of Preventive maintenance is the creation of a predictable maintenance schedule, which can improve safety and reduce costly downtime.However, this approach may lead to over-maintenance—servicing equipment more often than necessary—which in turn can elevate operational costs. It is also labor intensive. Preventive maintenance is structured around the who (declining trained technicians), what (scheduled maintenance tasks that can’t be completed), where (on all critical machinery), when (hopefully at predetermined intervals), why (to prevent failures), and how (through systematic inspections and maintenance protocols). With the declining manpower and maintenance teams stretched too thin, this approach is increasingly difficult to sustain.
What is Predictive Maintenance?
Predictive maintenance (PdM) refers to the practice of monitoring the health condition and performance of equipment during its normal operation to detect signs of potential failure. By leveraging Condition Monitoring technologies, Predictive maintenance allows for interventions only when necessary, thereby preventing downtime, putting labor time back on the clock, and saving costs.The benefits of PdM include reduced maintenance frequency, prevention of unexpected failures, and extended equipment life. However, challenges lie in the initial cost of setting up monitoring systems and the need for continuous data analysis. Predictive maintenance answers the who, what, where, when, why, and how of potential equipment issues before they become critical, ensuring maintenance efforts are precisely targeted and effective.
Predictive Maintenance vs Preventive Maintenance – What’s the Difference?
The fundamental difference between Predictive and Preventive maintenance lies in their approach and execution. While Preventive maintenance is scheduled based on time or usage, Predictive maintenance is condition-based and only performed when certain indicators show signs of decreasing performance or upcoming failure. This makes Predictive maintenance more dynamic and often more cost-effective as it is more tightly aligned with actual equipment needs rather than a fixed schedule.How to Measure Machine Health & Performance
Measuring machine health and performance involves many strategies and technologies including machine health monitoring, industrial equipment health analysis, and proactive maintenance. By continuously assessing the operational parameters of machinery, such as vibration, temperature, humidity, pressure, and acoustics, businesses can detect anomalies in otherwise normal trends that signify deteriorating conditions. This data-driven approach ensures that maintenance efforts are timely and accurately aligned with the machine’s actual condition, thereby optimizing depleted maintenance resources, and enhancing equipment performance.What Makes Trico Different
Implementing effective maintenance strategies can be complex, but companies like Trico provide specialized solutions that simplify this process. Trico differentiates itself with a robust offering of lubrication management systems and services that ensure optimal maintenance. By integrating sensor technology, such as those found in the Machine VitalsTM, Trico enhances Predictive maintenance capabilities, enabling real-time monitoring and simple analysis that preempt equipment failures.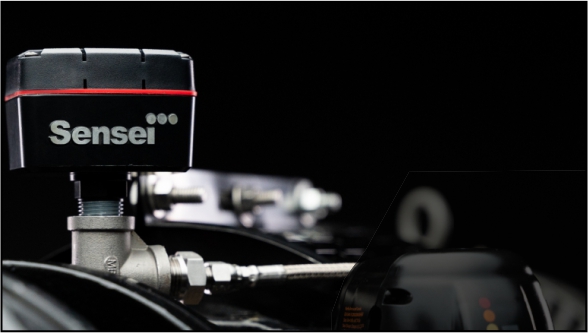
Trico's approach not only facilitates Predictive and Preventive maintenance but also tailors these strategies to meet the unique needs of each piece of equipment. The additional benefit of being a certified Oil Analysis laboratory, Trico’s Orbital Oil Analysis information is also integrated into the Sensei platform that machine Vitals uses to uniquely display data. Machine Health data, Oil Analysis information, equipment information, and maintenance event log information for all your equipment in one place. Now that's a powerful asset.
Both Predictive and Preventive maintenance are essential to an effective condition-monitoring strategy. Each has its strengths and plays a critical role in a comprehensive maintenance program designed to minimize downtime and extend the lifespan of machinery. The world is continually evolving from Preventive Maintenance to Predictive Maintenance for many reasons.
Choosing a complete solution partner is essential for successfully implementing a maintenance program in your facility. Call us today to get started.