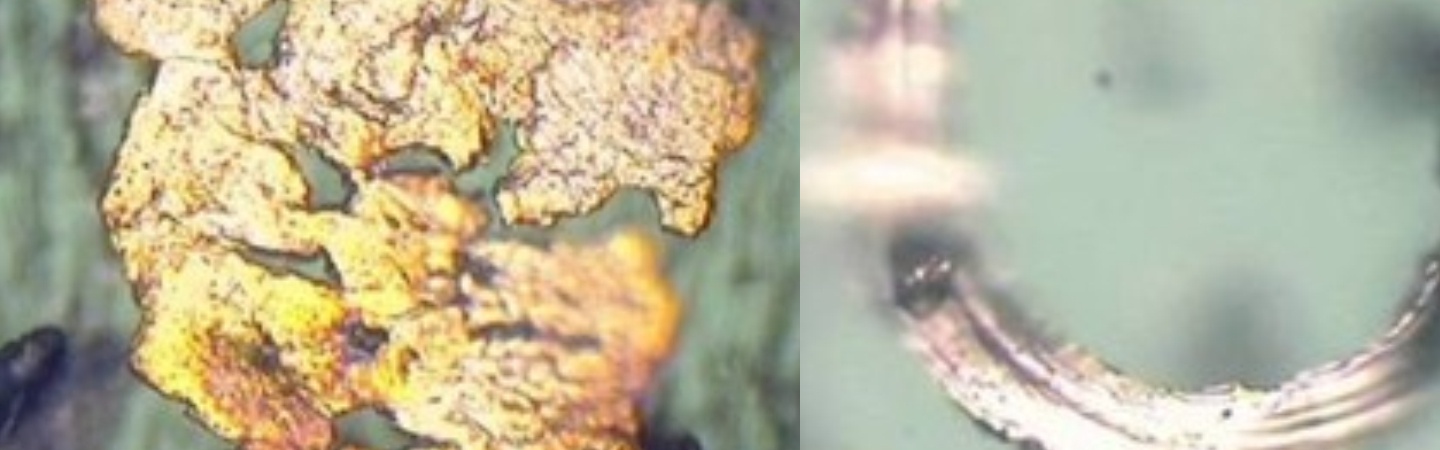
Mike Gauthier
11.10.2020
Utilize oil analysis to monitor particle counts and take advantage of products available to reduce them
For many years, it has been known that more than 75% of all machine wear related failures are due to particulate contaminants. All kinds of particles continue to find their way into the most critical locations of our machines. We have developed systems of measurements for particle counts, devices that measure particle counts, instruments that extract precise oil samples, and designed filtration equipment to remove these particles. Yet we continue to see failures. It is about time to take control of particulate problems. Below is a short guide to arm you with the information you need to take control and reduce your machine wear failures.
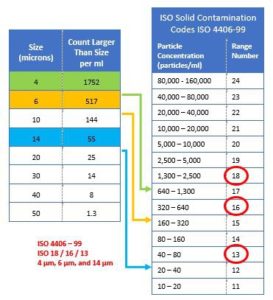
ISO Code – System of Measurement
The Solid Contamination ISO Codes were developed to provide a universal quantifier that represents a range of allowable particle contamination in a piece of equipment or system. This allows equipment manufacturers to specify how much contamination is acceptable in a concise manor. Each particle range doubles in quantity of particles as the ISO number gets larger. An ISO cleanliness code contains 3 numbers that represent the number of particles equal to or greater than a specific micron size. These sizes are 4-micron, 6-micron, and 14-micron. For example:
Particle Analyzers – Method of Measurement
Particle analyzers have come a long way. It used to be that these machines could only crudely provide an estimation of particle count. Today, these machines can take a very small sample of oil from a sample bottle and allow users to get a complete report of number, size, and shapes of particles. These shapes can further be used to classify the particles into different types of wear. This information is powerful to identify what kinds of particles are in the system, and perhaps where its coming from. This allows the user to make informed decisions on what corrective action to take before damaging levels can occur. These results are typically reported from an oil analysis lab, along with many other tests that make up the entire oil health story.
ISO Code – Oil Analysis Reports
To utilize the particle count results on an oil analysis report, it is important to first establish upper and lower limits of particles (ISO Codes) based on the equipment, environment, criticality, and the recommendations from the manufacturer. They provide a quick pass/fail for the particle counts in your equipment. It is also important to identify the number of particles the oil you started with before putting it into the equipment. This is known as a reference sample. Reference samples are taken from the container the oil is stored in and used as a baseline when comparing to current operational condition of the oil. Here is what it might look like on an oil analysis report:
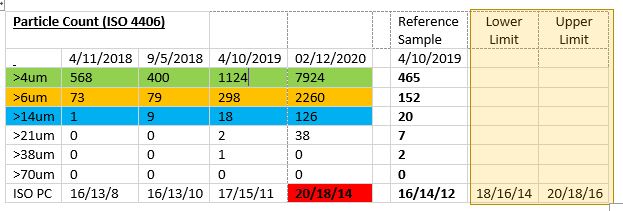
We can see from the report above, this customer has already established the upper/lower limits for this piece of equipment. We can also see that a reference sample was taken at the same time as the machine sample on 4/10/2019. The ISO code trend clearly shows something has happened to dramatically increase the oil’s particle count since taking the reference. This would indicate particulate is being generated within the equipment itself or entering the system from the atmosphere and/or process. The more reference samples you have along the storage and transfer stages of an oil’s lifecycle, the easier it will be to pinpoint when contaminants are being introduced.
ISO Code – How it Changes
Below are some of the areas that represent how easy it is to lose control of your particle counts from the time it arrives to the time it reaches your equipment.
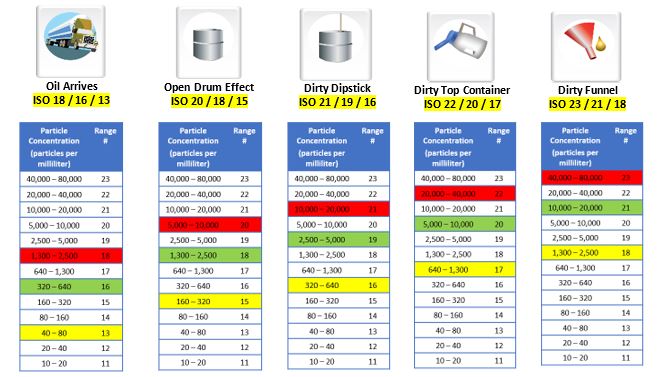
Once particulate is in your equipment, without being addressed, it becomes a snowballing effect. Particles continue to enter wear zones in the components and break apart, creating more and more particles.
ISO Codes Are Rising – Protect Equipment with Desiccant Breathers
Particle counts can rise for many different reasons. One of which is how the equipment, or storage tank, is vented to the atmosphere. If we reflect on the old school way, it was typically an open passage vent or a “goose neck” standpipe, or nothing at all. Today, the use of desiccant breathers are more prominent than ever, and for good reason. They work. Desiccant Breathers provide a means for equipment or storage tanks to breathe clean, dry air. Typically, these breathers contain a few 3-micron particle filters, carbon fume reducers, and water adsorbing desiccant. This not only protects your equipment from atmospheric particles that previously would work its way into the oil but keeps water out as well. This is an easy solution to reduce water and particle contamination from the surrounding environment.
High ISO Code/Particle Count – Filter them Away!
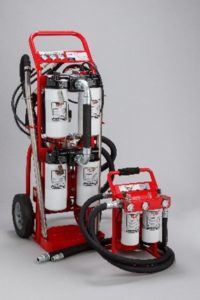
Regardless of how particulate enters equipment or system, there are a couple of ways to remove it. One is to change the oil and flush the system. But what if the oil reservoir is a couple hundred gallons, and the overall health of the oil is good? Chemistry and additives are fine, and a shutdown is not scheduled for months. Deploying a filtration system may be a suitable alternative to a change and flush. This can extend the oils useful life, reduce disposal costs, and save the valuable manhours necessary to perform the maintenance. Many years ago, your only option was to install large, permanent, very expensive palletize systems that were dedicated to one or a couple of machines. Today, there is a wide variety of portable filtration units that are versatile in their abilities to filter and offer flexibility on where they can be utilized. Vacuum dehydrators, centrifuge type systems, cannister style and spin-on filter systems are just some of the systems available today. If you are considering a system that incorporates filter elements, there are a couple items to note.
Filter size recommendations for equipment: The cleanliness level required in lubricating a hydraulic systems is determined by the most sensitive component. Most manufacturers of lubricants, industrial equipment such as pump and gearboxes, and hydraulic systems will specify the optimal cleanliness requirements for their own equipment. If not available, filter manufacturers will supply a more generalized ISO target recommendation chart based on equipment such as Hydac’s shown here. Furthermore, these recommended target ISO codes can be related to the micron size filter that will get you to achieve those targets.
- Comparing Beta Ratings: Beta ratios were developed specifically to compare the filtering efficiency of a filter media at a given particle size. These efficiencies can be plotted and a graph an overall average when Multi-Pass Testing. Filters should be compared for beta rating at the same given size. Be careful though. The higher the micron size the more efficient a filter becomes. So, for example if we look at the Trico 10 µm filter plot – it can actually be called out as a Beta9 ≥ 200 and/or Beta12 ≥ 1000. These types of charts need to be consulted when comparing beta ratings.
- Dirt Holding Capacity – Along with comparing the Beta Ratings of filters, you will want to compare the dirty holding capacities of the filters. This will tell you how much particulate a filter will hold and how well it retains particles. Compare the cost per gram of the filters.
Reducing Particulates in Lubricants
Over the past couple of decades, we have seen an entire industry grow in the area of oil analysis and overall protection of your oil. Products and services have been created and designed to help you protect your equipment from particulate. Utilizing oil analysis tools such as particle counts that are converted to ISO CODES are an effective measuring stick to monitor your equipment. Taking advantage of products available to you will greatly increase your success level when battling high particle counts and in the end, reduce your machine wear failures.