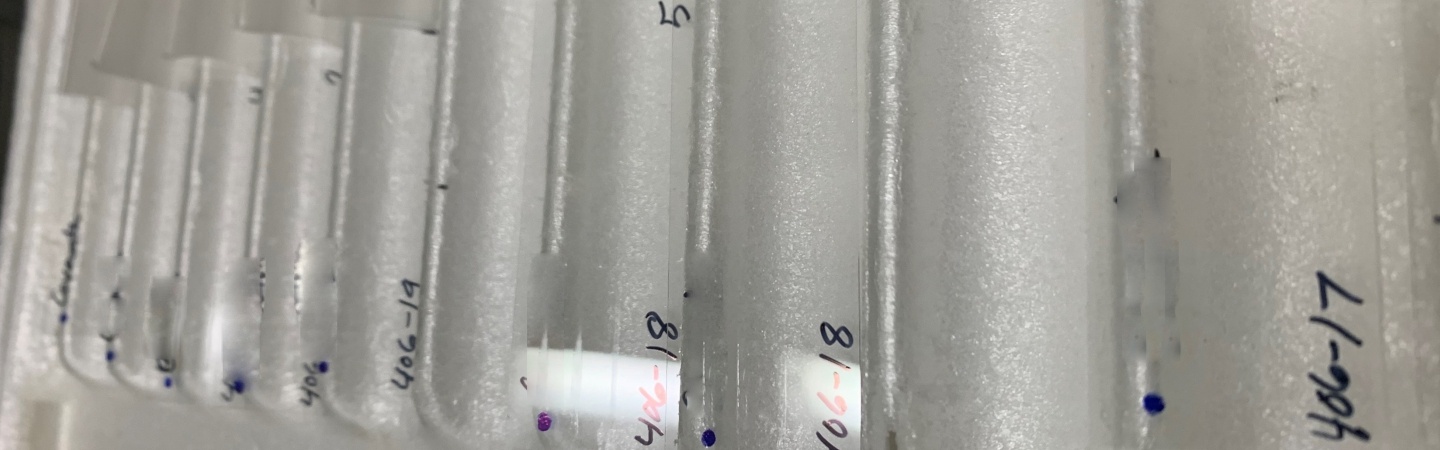
Dan Freeland
04.13.2021
Understanding a Ferrogram Maker
In a previous blog we discussed Wear Particle Counts (WPC) derived from the Dl and Ds numbers calculated by a Direct Reading Ferrograph (DR). We shed light on the importance of trending that number to detect initial stages of potential breakdowns, which certainly is helpful in terms of quantity of ferrous particles. But where are the particles coming from? What component(s) are beginning to fail? Today we will introduce the Ferrogram Maker (FM-6).
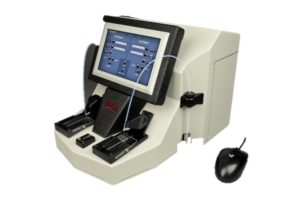
What is Ferrography?
Ferrography can is defined in Wikipedia as “a specialized type of oil analysis used to study particle wear on machine components through analysis of contaminants in lubricating oil. It can be used to predict and diagnose errors occurring on machinery”.1 When DR’s and/or other analysis indicate abnormal wear, analytical ferrography can further pinpoint its source and the specific type of wear with the power of a microscope.
What is a Ferrogram Maker?
To be able to look at the contaminates in a lubricating oil under a microscope, we must first have a way to systematically lay out particles on a slide, or in other words, create a ferrogram. This is the primary purpose for the Trico FM-6 dual Ferrogram Maker. To make controlled, methodical, ferrograms that allows very little particle stacking to occur. This allows trained analysts to extract, classify, and visually analyze wear particles and solid contaminants. Particles are examined to determine the size, concentration, color, shape, and particle composition. Results received from the analytical ferrography provide for the application of timely, corrective maintenance, based on a machine’s actual condition.
How does the FM make a Ferrogram?
The Ferrogram Maker magnetically separates machine wear debris from the lubricating oil. The oil sample is first diluted for improved particle precipitation and adhesion. The diluted sample flows down a tube on a specially designed glass slide called a ferrogram. The ferrogram rests on a magnetic block, which attracts ferrous particles out of the oil. Due to the magnetic fluid, the ferrous particles align themselves in chains along the length of the slide with the largest particles being deposited at the entry point. Nonferrous particles and contaminants, unaffected by the magnetic field, travel downstream and are randomly deposited across the length of the slide. After the particles are deposited on the ferrogram, a wash is used to remove any remaining lubricant. The wash quickly evaporates and the particles are permanently attached to the slide. The ferrogram is now ready for optical examination using a Ferroscope.
Who uses FM’s?
Ferrogram Makers are used in most reputable oil analysis labs as a tool for creating slides for analysis. Many companies with very expensive critical equipment have their own labs in house that also utilize the FM instrument. When comparing the potential cost of critical equipment catastrophic failure and downtime, the cost of these oil analysis tools can be completely justified. If you are considering a move to an internal lab, make sure you have personnel who is educated in Analytical Ferrography. There are several classes out there, including our own at Trico Corporation, to learn the craft from industry leaders and be given the knowledge and resources to successfully interpret ferrograms internally.
For additional information on Ferrogram Makers, follow the links below.
- To learn more about the features and benefits of the FM-6 Ferrogram Maker click here.
- To learn more about Trico’s Analytical Ferrography Training click here.
- To see a video of the FM-6 and its operation click here.
Have questions regarding the Ferrogram Makers or analytical ferrograpy, we are here to help.
- Category:
- Oil Analysis
- Contamination