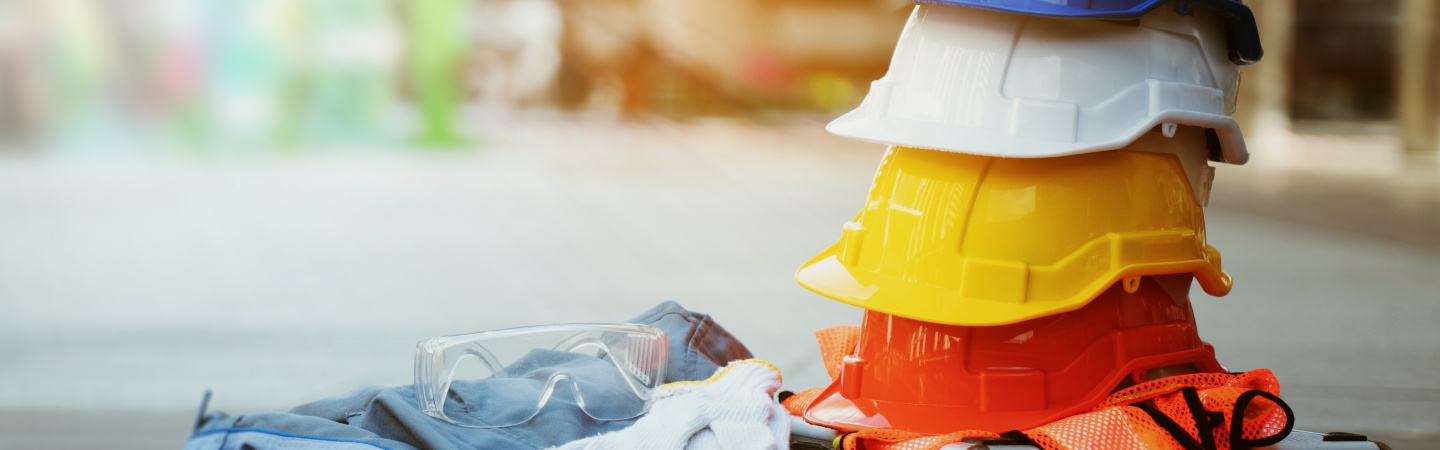
Dan Freeland
10.15.2024
Addressing Labor Shortages with Machine Vitals
Labor shortages have become a growing concern across multiple industries, especially when it comes to equipment maintenance. With a shrinking pool of qualified workers, companies are finding it increasingly difficult to meet the demands of regular inspections and upkeep. Automated solutions like Machine Vitals are stepping up to the plate, reducing the need for manual inspections and streamlining essential maintenance tasks.
The Escalating Labor Shortage in Maintenance
Across the globe, industries are dealing with an alarming shortage of skilled labor, particularly in technical maintenance roles. A perfect storm of an aging workforce, difficulty in attracting younger talent, and high turnover rates have created a widening gap between the need for regular equipment maintenance and the workforce available to perform it. In the U.S. alone, over 25% of maintenance personnel are expected to retire within the next decade, while job openings in the field are projected to increase by 10% over the same period. Meanwhile, a Deloitte study reports that 2.1 million manufacturing jobs could go unfilled by 2030 due to skill shortages, many of which involve maintenance roles.
The Domino Effect: How Labor Shortages Impact Equipment Reliability
When maintenance teams are understaffed, equipment reliability inevitably takes a hit. Preventive maintenance schedules get delayed, inspections are missed, and minor issues that could be easily fixed can spiral into major, costly breakdowns. This results in increased downtime, higher repair costs, and further strain on the remaining maintenance staff. 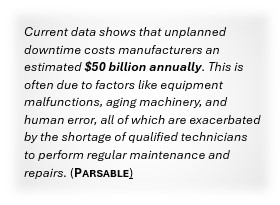
Overworked Technicians: With labor shortages pressing on, the remaining maintenance technicians are shouldering heavier workloads, often putting in significant overtime just to keep operations running. A 2022 report by the U.S. Bureau of Labor Statistics found that nearly 50% of maintenance workers now work more than 40 hours a week, with manufacturing maintenance staff averaging over 5 hours of overtime weekly.
This uptick in overtime comes with a price. According to the National Safety Council, working beyond 60 hours a week increases the risk of workplace injuries by 23%—a dangerous prospect in the demanding environments where maintenance personnel typically operate. As workers grow fatigued, errors in judgment and missed inspections become more frequent, leading to further equipment degradation.
Moreover, burnout is taking its toll. 61% of technical staff reported burnout due to excessive overtime, according to an Aon survey. This not only leads to higher turnover but exacerbates the very shortage of skilled labor that led to the overtime in the first place. With fewer technicians available, companies are increasingly relying on stopgap measures like overtime to stay afloat—a strategy that is ultimately unsustainable.
How Machine Vitals Minimizes the Need for Manual Inspections
Enter Machine Vitals: an automated condition-monitoring solution designed to ease the burden on maintenance teams. By continuously tracking key parameters, Machine Vitals ensures that equipment stays in optimal condition without the need for frequent manual inspections. 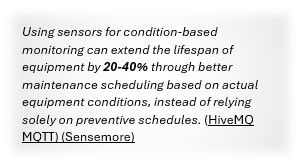
Early Detection of Issues: The continuous data stream provided by Machine Vitals enables early detection of equipment wear and degradation. Instead of waiting for scheduled maintenance intervals (that may be missed or delayed anyway), teams are alerted to potential problems as soon as they arise. This proactive approach helps catch small issues before they become costly failures, reducing the need for time-consuming manual checks.
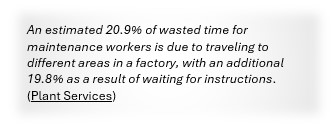
Long-Term Benefits of Automated Maintenance Solutions
As labor shortages persist—and in some cases worsen—the reliance on automated maintenance solutions like Machine Vitals is undoubtedly going to increase. By automating routine inspections and enabling more efficient use of existing staff, companies can maintain equipment reliability without being hamstrung by a shrinking workforce. Automated systems also provide a significant boost to predictive maintenance efforts, where data trends can forecast future failures before they happen. This is a huge advantage for industries that rely on minimal downtime to remain competitive.