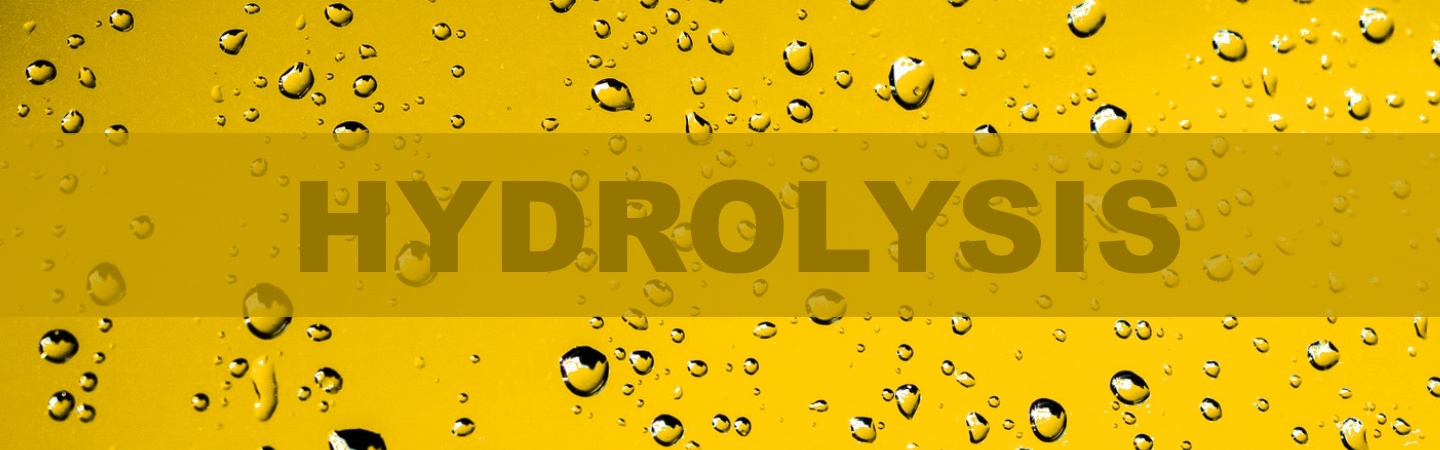
Victoria Bunchek
05.12.2020
Spring Increases Risks of a Harmful Chemical Reaction in Your Machinery Oil
Take it from the 55% of lube professionals who’ve seen the harsh effects of hydrolysis: you really don’t want this chemical reaction in your equipment.
Hydrolysis in machinery lubricant can cause permanent degradation of your oil, rust in your machines, even total equipment failure.
This chemical reaction happens when water works its way into your machines, which is more likely when ambient humidity rises, like in springtime. That’s why now is the time to get a handle on this threat – especially if humidity is already an issue in your area or your industry.
How Hydrolysis Happens
Hydrolysis is primarily a concern with certain synthetic lubricating oils, in which hydrolysis can form destructive acids while causing other changes to the oil’s viscosity and other key physical and chemical properties. However, it can also occur to a lesser degree in other oil types. It is important to focus on not only the highly vulnerable synthetic ester fluids, but some of the other oil types as well – and more importantly, how to prevent it from happening at all.
We don’t normally think of it as such, but water is a highly reactive chemical (think about how it dissolves sugar, salt, and ruins your wood furniture). Some materials are more susceptible to water’s attacks than others (good luck cleaning up grease with just water). All oils are a mixture of susceptible and less susceptible materials, so some will be more affected by water than others. If water is present in vulnerable lubricants the bonds will begin to break, especially at higher temperatures, destroying the lubricant and harmful acids will be unleashed in your system.
In simple terms, that’s hydrolysis.
OK, So What’s the Most Effective Way to Stop Hydrolysis?
If you suspect excessive water or the risk of hydrolysis in your machinery oil, you should certainly get a sample tested.
As discussed earlier, some lubricant formulations can withstand more water contamination than others – an attribute called hydrolytic stability.
The way to prevent hydrolysis, however, is to keep unintended water out of your lubricant.
Water contamination can occur in many ways throughout the Journey of the Lubricant in your facility.
At the machine, it’s important to close off every possible water ingression point. Vented oilers remain a common way for water to infiltrate rotating equipment, so you may want to look into closed system oilers.
Create a Hydrolysis Plan of Action
We can help you implement a quick plan of action to prevent water contamination and monitor for hydrolysis. Click below to request free counsel from a lubrication consultant at Trico.
- Category:
- Oil Analysis
- Contamination