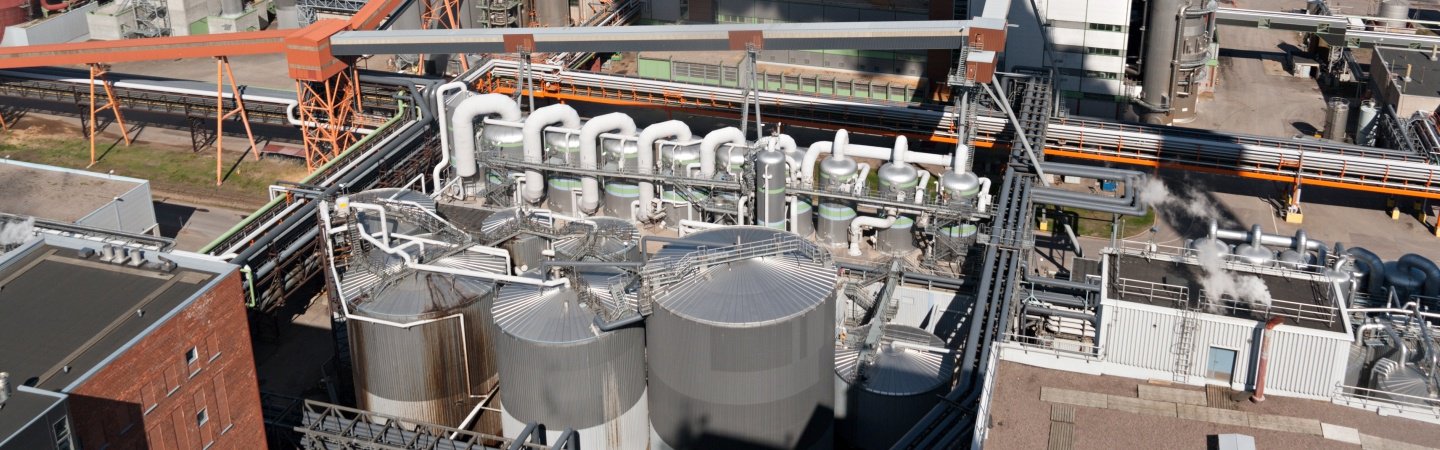
Lisa Kiepert
08.29.2023
The Importance of Condition Monitoring and the Role of Oil Analysis
In today's fast-paced industrial landscape, maximizing equipment reliability is paramount for businesses seeking to minimize downtime, reduce maintenance costs, and enhance operational efficiency. One crucial tool that enables proactive maintenance practices is condition monitoring, with oil analysis emerging as a key component in this process.
Understanding Condition Monitoring
Condition monitoring involves the continuous assessment and tracking of equipment health to identify potential failures before they occur. By using various techniques such as vibration analysis, thermography, and oil analysis, organizations can gain valuable insights into the condition of their machinery, enabling timely and targeted maintenance interventions. Among the different approaches, oil analysis stands out as a reliable method for extracting critical data about the internal health of machines.
The Role of Oil Analysis
Oil analysis is the process of examining lubricant samples to assess their physical and chemical properties. By analyzing oil samples from equipment, technicians can detect signs of wear, contamination, and other potential issues that may compromise performance. Here are some key factors in which oil analysis supports effective condition monitoring:
-
Early Detection of Equipment Degradation: Monitoring the condition of oil allows technicians to identify early signs of equipment degradation, such as increased wear metals or the presence of contaminants. By catching these issues early on, maintenance teams can intervene promptly, preventing costly breakdowns and minimizing unplanned downtime.
-
Optimized Maintenance Intervals: Oil analysis provides insights into the condition of the lubricant, allowing for optimized maintenance intervals. Rather than relying solely on fixed schedules, maintenance activities can be scheduled based on actual equipment condition, reducing unnecessary maintenance and extending equipment life.
-
Improved Equipment Performance: Clean and well-lubricated equipment operates more efficiently, leading to improved productivity and reduced energy consumption. Regular oil analysis helps identify lubricant degradation and contamination, enabling timely oil changes and maintenance interventions, ultimately enhancing equipment performance.
-
Cost Savings: Proactive maintenance strategies driven by oil analysis can result in significant cost savings. By identifying potential issues early on, businesses can avoid major repairs, reduce equipment downtime, and improve overall equipment reliability. Additionally, optimized maintenance intervals based on oil analysis can minimize the use of resources, such as replacement parts and lubricants, resulting in long-term cost savings.
Condition monitoring, with oil analysis as a crucial component, empowers organizations to adopt proactive maintenance practices and maximize equipment reliability. By harnessing the power of data provided by oil analysis, businesses can detect potential failures early, optimize maintenance intervals, enhance equipment performance, and achieve substantial cost savings. Embracing this holistic approach to condition monitoring paves the way for improved operational efficiency, reduced downtime, and a competitive edge in today's dynamic industrial landscape.
For more information on Oil Analysis, feel free to reach out to us.