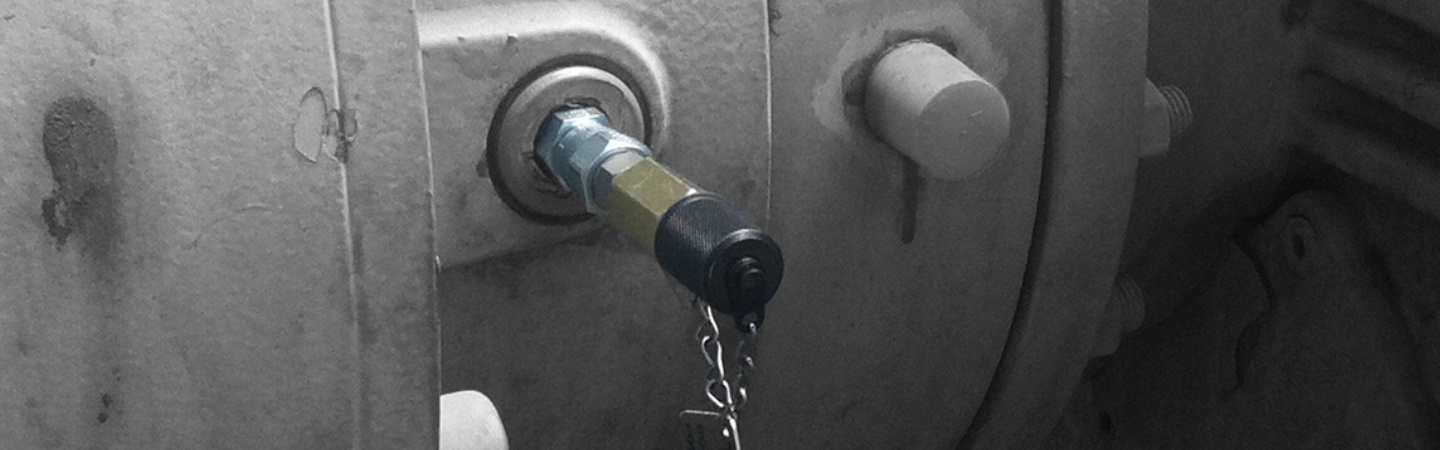
Lisa Kiepert
08.01.2023
Ensuring Reliable Results and Preventing Costly Failures
Oil sampling is a critical component of preventive maintenance programs for machinery and equipment that uses lubricating oils. Proper oil sampling provides valuable insights into the condition and health of the machine or equipment, allowing early detection of potential failures and reducing costly downtime. However, it is essential to flush out the line before obtaining an oil sample to ensure accurate results.
Flushing helps to remove any contaminants and residual oil from the system, ensuring that the sample collected is representative of the current condition. It is recommended to flush five to ten times the dead space volume in the line before taking the sample. Neglecting to flush the line can result in cross-contamination, leading to inaccurate results, and potentially causing more significant problems. By properly flushing out the line prior to sampling, operators can get a clearer picture of the machine's health and take appropriate actions to address any concerns.
Below is a chart of suggested flushing requirements.
