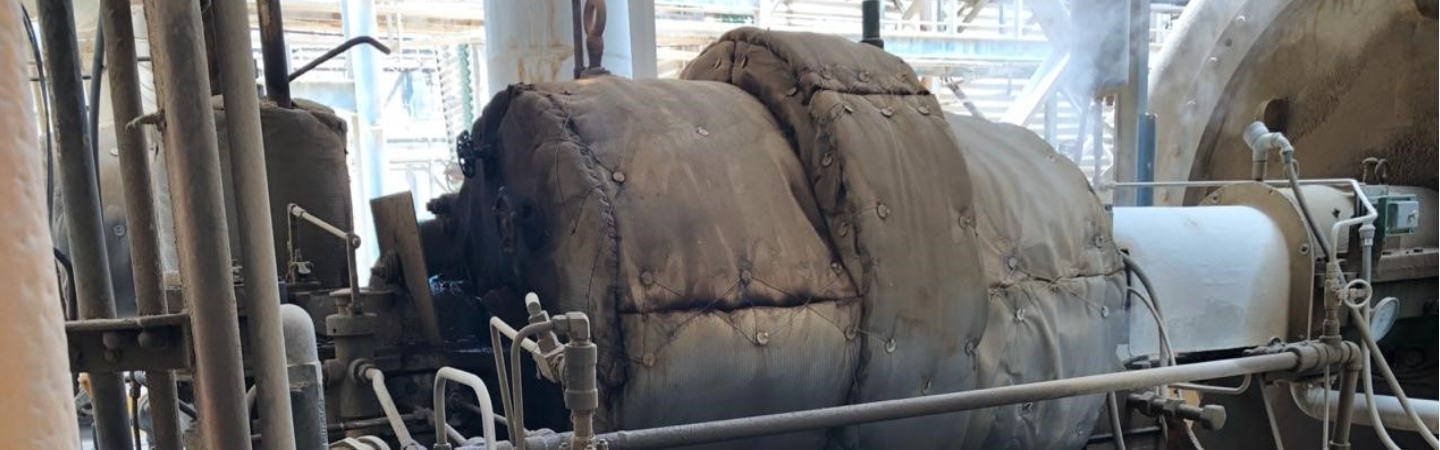
Victoria Bunchek
09.01.2020
Extending Oil Change Intervals
Should you use oil analysis to determine when to change your oil, or does a scheduled interval approach work best?
Quite a few companies today are performing oil changes on a scheduled interval approach. It is typically based on an assortment of factors such as timeframe and operating hours. However, this approach wastes millions of gallons of oil prematurely that still may have useful life.
Condition-based oil changes which utilizes oil analysis to determine the useful life is gaining in popularity because of the reduction in oil consumption and the costs associated with oil changes. In addition, the results from oil analysis is used to direct maintenance activities allowing mechanics to focus on tasks that are necessary.
Because of this, we are seeing more companies making the switch to condition based oil changes. One of the most recent ones, is a chemical plant in Mexico who switched from scheduled interval to condition-based oil changes on their critical blower.
Cost of Scheduled Interval Oil Changes
The chemical plant was changing oil on their critical blower every 4 months – based on the manufacturer’s recommendation to help prevent equipment breakdown due to degradation of lubricant quality and performance.
Unfortunately, changing the lubricant in the blower is extremely costly and time consuming. Each oil change takes 2-3 days and requires 211 gallons (800 liters) of lubricant at a cost of $1,180 per 55-gallon drum. That’s a total cost of $4,526 in lubricant alone!
This does not include the many other hidden costs associated with each oil change.
- Oil change time/man hour costs
- Consumable supply costs
- Downtime/lost production costs
- Waste/disposable cost
Oil Analysis and Filtration Working Together
Due to the costs and time associated with each oil change, the chemical plant enlisted the help of a Trico Distributor to extend the oil change intervals on the blower.
The first thing was to determine the current condition of the oil and equipment through oil analysis. The mechanics at the chemical plant extracted a sample of lubricant and sent it to Trico. The results revealed elevated levels of particulate contamination.
To reduce the contamination levels, a filter cart was purchased from the Trico Distributor with a 3-micron filter.
Once filtration was complete, another sample was extracted from the blower. The results indicated a significant decrease in the particulate levels, allowing the chemical plant to skip the oil change.
Particle Count (ISO 4406)
Before | During | After | |
>4um | 9637 | 3888 | 913 |
>6um | 4093 | 1401 | 189 |
>14um | 298 | 92 | 9 |
>21um | 63 | 30 | 3 |
>30um | 1 | 1 | 0 |
>70um | 0 | 0 | 0 |
ISO PC | 20/19/15 | 19/18/14 | 17/15/10 |
Extending Oil Change Intervals
The chemical plant continued this practice, on the blower, and kept seeing favorable results from oil analysis and filtration.
Plus, the filter cart allowed the chemical plant to filter the oil while the equipment was running, with minimal effort from the mechanics – freeing up their time for other projects in the plant. Due to the success and benefits received, they have extended this practice to other critical equipment within the plant.
Switching to condition-based oil changes has proven to be beneficial to the chemical plant’s bottom line. It has reduced equipment downtime, extended oil change intervals and reduced oil change costs and the associated costs of them. In the first year, the filter cart has paid for itself and the entire oil analysis program…a small investment made for long term benefits.