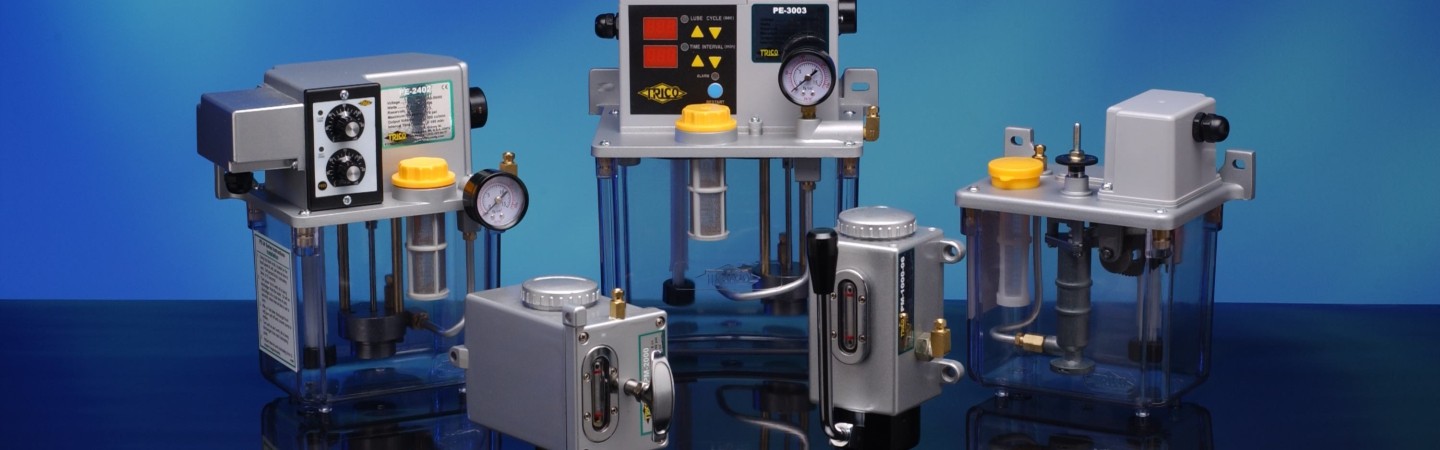_1.jpg)
Lisa Kiepert
01.31.2023
Preventing wear and tear on machine components
Central Lubrication Systems are used in many different types of equipment, offering an array of benefits that can help protect and prolong the life of the equipment’s moving parts. Common applications include punch presses, milling machines, printing presses, injection molding machines, CNCs, and more.- Increase machine efficiency and productivity
- Extends service life of equipment
- Prevents costly downtime
- Reduces lubricant waste
- Allows the right quantity of lubricant be administered
The systems use a pump and metering devices to provide a precise amount of lubricant to the equipment components, allowing them to stay adequately lubricated. This reduces wear and tear on the components while also improving their ability to withstand the harsh conditions they operate in.
There are a variety of systems available. But how do you choose the right one? It’s important to consider all the options available before making the decision as each system has its own unique features. To help with the decision-making process view this short video on the different systems available.
Need assistance?
If you’re unsure whether or not a Central Lubrication System is right for your application, please contact us for assistance.
- Category:
- Lubrication Program
- Tags:
- Central Lubrication