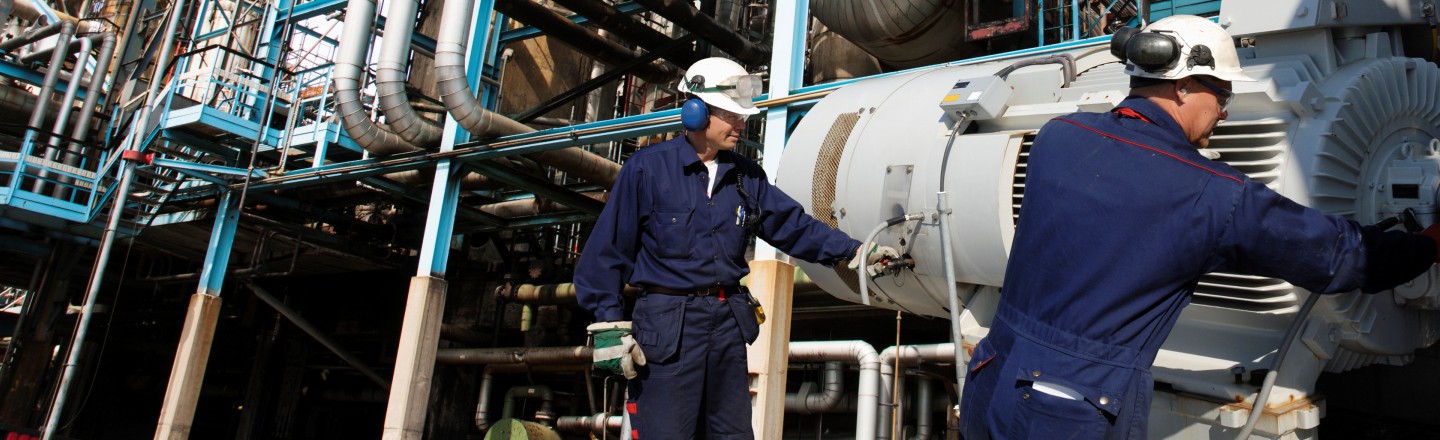
Mike Gauthier
06.22.2021
Reducing Friction Between Maintenance and Operations Over Lubrication Tasks
Does the relationship between your operations and maintenance personnel run in greased grooves, or is more like the Hatfields and McCoys? The friction between them can get intense when one side accuses the other of failing to support its mission. Ways to ease this tension include learning how to communicate better, developing standard operating procedures, providing training and using IIoT technology. As a result of Operational Driven Reliability (ODR) initiatives that became popular about a decade ago and given the COVID pandemic facilities must do more with less. Because of their proximity, machine operators were asked to handle tasks that were previously the domain of maintenance, such as checking oil levels and lubricating machines. Unless handled properly, however, seemingly simple requests could lead to conflict and inefficiencies.
Friction Point #1: Department culture wars
The first issue might be cultural in nature, as identities of personnel in each department strongly correlate with their responsibilities or tasks for which they trained and were originally hired to perform. In short: operators operate equipment, maintenance personnel keep it running. Effective change depends on how maintenance approaches operations. Here are two steps to help stop culture wars and inspire collaboration:
- Get on the same page. First, both parties need to agree that a new reality exists: maintenance is stretched too thin to perform all of its traditional tasks and achieving uptime and associated production goals depends on collaboration. This can help short circuit a “not my job, not my problem” attitude. Also, consider that some operators might feel as if they’re taking work away from their “brothers in maintenance,” and that is not the case.
- Get to yes. Joint discussion and decision-making are vital to ensure that everyone’s voice is heard and accounted for. There are some excellent tips in a Harvard Negotiation Project book titled Getting to Yes. This book emphasizes an approach they call “Principled Negotiation.” The idea is that a negotiation can be tough on a particular problem, but soft on the parties involved.
- A great way to get the two departments to work smoothly together is to involve one-another in the decision-making processes. In order to reach a consensus, both sides need to be heard, and need to listen. Then interests need to be identified, through asking questions, and relating in any way possible. After both party’s feelings and ideas have been identified, the group can continue on by brainstorming and attempting to find a mutual gain. Through this way of negotiating when departmental decisions need to be made, employees are much more likely to be understanding and have a positive attitude about the changes at-hand.
Friction Point #2: Not So Simple
Lubrication might seem simple, but using untrained personnel can open the downtime floodgates. Some all-too-real scenarios include:
- Untrained personnel think “oil is oil” and top-off the oiler using the nearest lubricant, inadvertently using a lubricant with the wrong viscosity or mixing a mineral with a synthetic oil
- Simply topping off an oiler daily — and never informing maintenance of a leak
- Over-filling, which could lead to foaming and an insufficient lubricant film, plus oilers need headspace to apply sufficient pressure and function properly
- Using makeshift transfer containers or funnels that introduce contaminants
- Over-greasing (“playing it safe”), which increases resistance and prematurely wears bearings
It’s critical to address these issues with four steps:
- Develop SOPs. To prevent friction over lubrication tasks, develop and document standard operating procedures and then training all essential employees helps.
- Select lubrication sites. To further reduce mistakes, establish satellite lubrication areas in proximity to operators — and be sure to involve operators when selecting locations.
- Stock right. Stock lube rooms with color-coded and shape-coded tags to link lubricant containers to application points. Don’t forget to provide single-use funnels and tubing.
- Use technology. Of course, the best way to solve a problem is to eliminate its source. Checking oil levels can be tedious, possibly dangerous or difficult depending on the situation, and it adds no value if the oil level is acceptable. Instead of asking operators to inspect oilers, consider IIoT-enabled devices like Trico’s Sensei® Enabled Opto-Matic Oiler that provide real-time oil level readings with data via a browser-based application. Using technology satisfies the needs of all parties, and it frees scarce maintenance time for other critical functions.
Grease the wheels of collaboration
Reducing tension between your operations and maintenance personnel sets in motion plenty of interconnected improvements. You’ll see better communication, fewer conflicts, more efficient use of lubricators and advanced technology, and improved overall operations. Get started with simple changes that can lead to significant benefits throughout your facility.
Understand What Sensei Can Do For You
- Category:
- Application