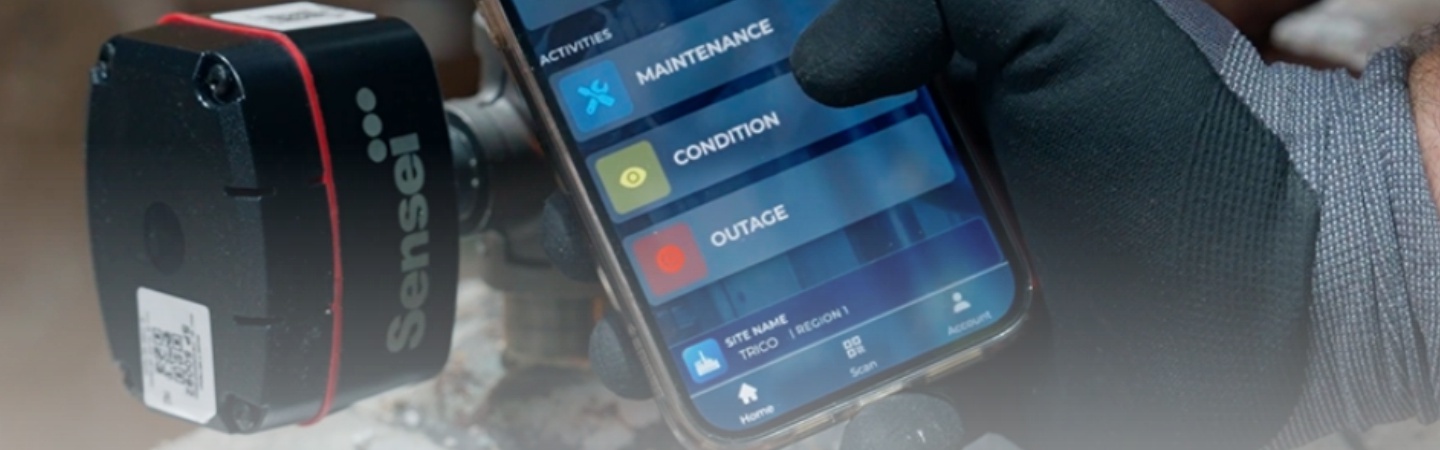
Dan Freeland
09.17.2024
Big Data, Lubrication, and Why Your Machines Will Thank You
Imagine your machines c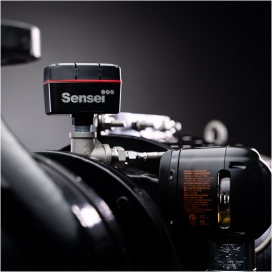
Gone are the days of changing oil based on guesswork or sticking to a rigid schedule that doesn’t account for actual wear and tear. Today, we’re talking predictive maintenance, where AI does the heavy lifting—analyzing vast amounts of data and telling you when to top off the oil or when your machine is waving a tiny white flag that says, “Help me before I break down!” So, buckle up as we dive into the world of AI-driven lubrication management and why it’s the smartest way to keep your equipment running smoothly.
AI and Lubrication: A Match Made in Machine Heaven
If you’ve ever tried to guess the right time to change your car’s oil by smell (please don’t), you’ll know that guessing isn’t always the best strategy for machinery maintenance. For industrial equipment, it’s even worse. Poor lubrication is one of the leading causes of machinery failures, yet many companies still rely on periodic checks or just wait for something to go wrong. Enter AI, the hero we didn’t know we needed but now can’t live without.AI doesn’t guess; it knows. It takes in data from all sorts of sensors—measuring everything from temperature and pressure to vibration and even the chemical composition of your oil. It then runs this data through sophisticated algorithms (“fancy math”) and gives you insights you wouldn’t have picked up on until it was too late. Essentially, AI is the friend who tells you, “Hey, maybe don’t drive another 5,000 miles on that oil.”
Here’s where AI shines:
- Predicts Lubricant Health: AI analyzes data to predict when your oil is starting to go bad, long before you’d notice a problem. So instead of waiting until your bearings are howling, you can fix things early.
- Optimizes Oil Changes: Forget about those “every six months” oil change schedules. AI lets you know the optimal time to swap out your oil based on actual usage, not just some arbitrary date on a calendar.
- Prevents Catastrophes: By keeping an eye on things like vibration or temperature spikes, AI can warn you when something’s about to go very wrong—kind of like having a crystal ball, but way more practical.
Big Data: The Backbone of AI’s Brilliance
Alright, let’s get one thing straight—AI isn’t magic (although it can feel like it). It works because of big data. Think of your machines as relentless chatterboxes. They’re constantly talking to the sensors you’ve installed, saying things like, “It’s getting hot in here” (temperature data) or “I’m feeling a little shaky” (vibration data). These sensors pick up all that information, and if you tried to listen to it all yourself, your head would explode. This is where AI comes in—it listens to all that chatter for you and picks out the important stuff.Here’s a breakdown of the kinds of data AI thrives on:
- Vibration Data: Sudden increases in vibration? That’s usually your equipment’s way of saying, “I’m not well.” AI knows this and flags it as a warning sign, often related to lubrication issues.
- Temperature, Humidity, and Pressure Data: Just like a fever tells you something’s off in your body, elevated temperatures in machinery signal potential lubrication failures. AI catches these “fevers” early on.
- Oil Composition Data: Is there water in your oil? AI can tell you. Is your oil turning into sludge? AI will know. It analyzes chemical changes in your oil and tells you when it’s time for a replacement.
Where AI is Making Waves in Lubrication
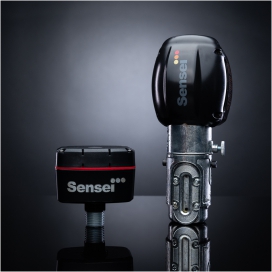
1. Optimized Oil Changes
Gone are the days of changing oil just because “it’s that time again.” AI systems take real-time data from your equipment, and oil analysis data, to tell you when your oil needs changing. This saves money, reduces waste, and—most importantly—prevents costly breakdowns.
2. Contamination Detection
Ever had a machine break down because water or dirt got into the oil? It’s a pain. AI and oil analysis data can detect contamination before it becomes a problem, giving you a heads-up to change the oil or add a filtration step before your machinery suffers.
3. Failure Prediction
Remember when predicting the future was something only fortune tellers did? Now, your machines can do it. AI learns from past failures and picks up on the subtle signs that mean trouble is brewing. If your machine is about to have a lubrication-related breakdown, AI will let you know well before things go sideways.
4. Improved Efficiency
When equipment runs smoothly, it doesn’t need to work as hard. With AI keeping lubrication at optimal levels, your machines will consume less energy, operate more efficiently, and generally last longer—meaning fewer emergency repair calls and a lot less downtime.
Looking Ahead: Digital Twins and IIoT—AI’s Cooler, Techier Siblings
Just when you thought AI couldn’t get any better, we’re entering the era of Digital Twins and the Industrial Internet of Things (IIoT). No, these aren’t sci-fi terms (though they sound like it). Digital twins are virtual replicas of your machines that run in parallel to the real thing. These digital versions simulate everything happening to your equipment, using real-time data. So, not only can AI predict lubrication issues—it can simulate how they’ll affect your machine’s overall health and performance. For example, let’s say you have a hydraulic pump operating in a high-temperature environment. The digital twin can show you how prolonged exposure to heat will affect the oil’s viscosity, and AI can then recommend tweaks—like switching to a higher-viscosity oil or adjusting your cooling system.
Then there’s IIoT. This tech connects everything—the machines, the AI, the sensors, the oil analysis, and even the people in charge. Imagine getting a notification on your phone that your gearbox needs more lubrication. Yep, that’s what IIoT does. It takes the guessing out of maintenance by keeping everything connected and running like clockwork.
Challenges to Consider (Because It’s Not All Sunshine and Lubrication)
Of course, no technology is without its hurdles. Here are a few things to keep in mind when jumping into AI-driven lubrication management:
- Data Overload: AI needs a lot of data to work effectively. If your sensors aren’t up to the task or the data is inconsistent, AI will struggle to make accurate predictions.
- Costs: While AI can save money in the long run, the upfront costs for sensors, software, and implementation can be significant. But trust us, it pays off when your equipment stops breaking down every other week.
- Time: It does take time for AI to learn. It also takes time for users to understand just what and how AI is communicating.
- Skills Gap: AI requires specialists who understand both machine learning and maintenance. So, you might need to train your team or bring in some external experts to get things rolling smoothly.
Why AI-Driven Lubrication Is the Future (and the Present)
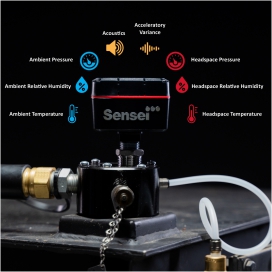
So, while your machines may not literally whisper “thanks” when you keep them properly lubricated, rest assured they’ll be running smoother, lasting longer, and saving you a lot of stress. And who knows? With AI evolving so fast, one day, you might just get that emoji-filled text from your gearbox.