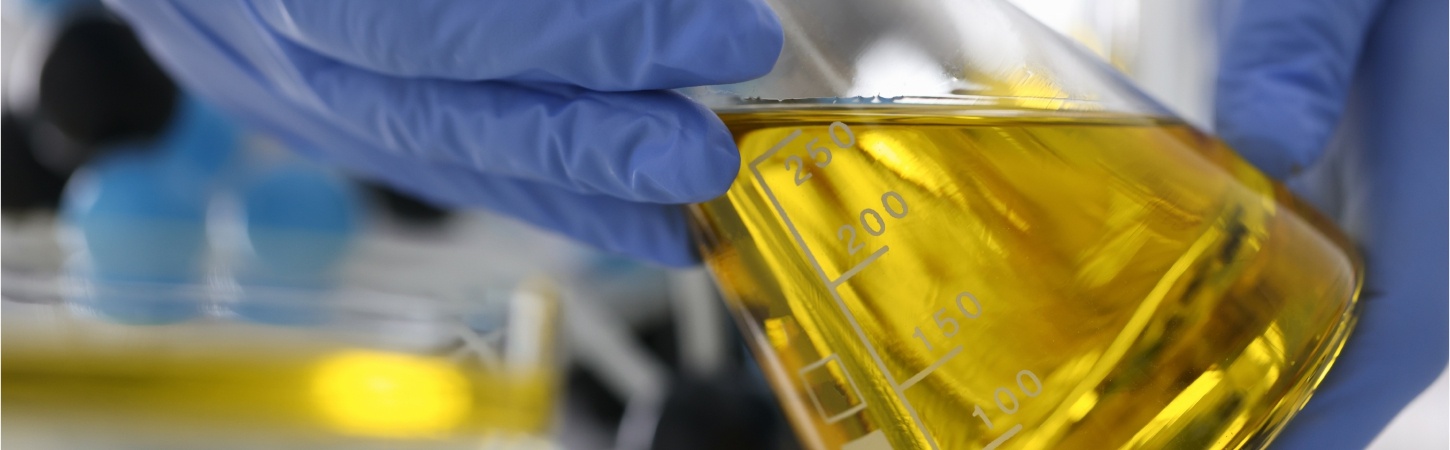
Dan Freeland
05.16.2023
The Power of Industrial Oil Analysis and Sampling
Maintenance is vital to keep industrial equipment running at peak performance without causing any disruption to manufacturing processes. One of the most significant expenses in maintenance is equipment downtime, which can range from hours to days or even weeks depending on the problem. Unplanned maintenance is often reactive maintenance, where repairs are made after a failure or breakdown has already occurred. This approach can lead to significant drawbacks, including reduced productivity, increased downtime, and higher labor and material costs. Fortunately, advancements in industrial oil analysis and oil sampling processes and equipment can help transform maintenance programs from reactive to predictive. In this blog post, we'll discuss the benefits of this shift and how to achieve it.
Understanding Reactive Vs. Predictive Maintenance
Reactive maintenance is often used when the focus is on fixing an issue in equipment after a problem has already occurred. This type of maintenance falls short, as it does not address the source of the problem but instead reacts to it after the fact. On the other hand, predictive maintenance is a proactive approach that uses the latest technologies and tools to anticipate potential problems before they happen. One of the most cost-effective ways to achieve predictive maintenance is through industrial oil analysis and oil sampling processes.
Advancements in Industrial Oil Analysis and Sampling
Modern industrial oil analysis and sampling processes use advanced techniques to provide more comprehensive testing and analysis of equipment. With the help of machines and sensors, experts can collect and analyze data about equipment conditions, temperature, vibrations, and fluid characteristics. They can predict failures before they happen, provide root cause analysis for maintenance issues, and offer valuable preventive maintenance advice.
Benefits of Predictive Maintenance
The benefits of predictive maintenance are clear. Predictive maintenance means fewer breakdowns, reduced unplanned downtime, and extended equipment lifecycles. Additionally, a proactive approach to maintenance translates to better planning, fewer emergency repairs, and reduced overall maintenance costs. By identifying and addressing potential problems before they happen, predictive maintenance can provide a competitive edge for businesses.
Implementation of Predictive Maintenance
For predictive maintenance to be successful, it requires a combination of the right tools, techniques, and human expertise. It involves frequent oil sampling, analysis, identifying equipment issues, and taking corrective measures. It is highly recommended to partner with an experienced service provider who can provide ongoing consultations, support, and insights. Regular data collection and analysis will help to fine-tune maintenance practices, identify potential problems promptly, and provide a proactive approach to maintenance.
The Future
Predictive maintenance is the future, and companies who shift from reactive maintenance to predictive maintenance will benefit from increased operational efficiency and profitability. With the right tools and expertise, predictive maintenance offers a more proactive, cost-effective approach that can predict issues before they occur, increase equipment reliability, avoid unplanned downtime, and optimize life-cycle costs. It is time for businesses to include industrial oil analysis and oil sampling in their maintenance programs and reap the benefits. Contact us to see how we can help take your maintenance programs to the next level.