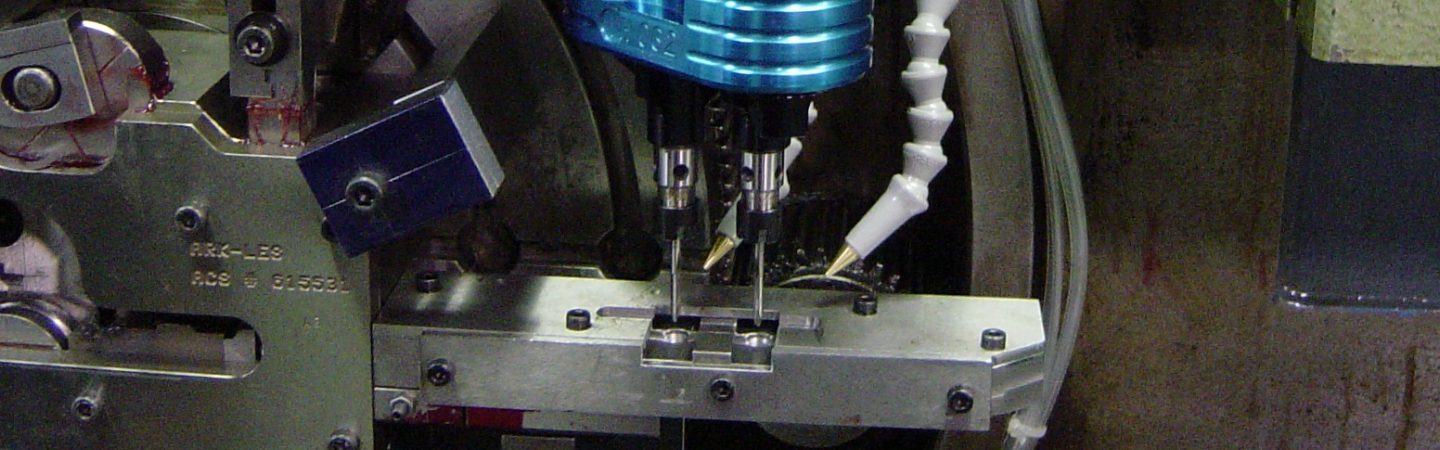
Dan Freeland
08.17.2021
Improving metal cutting operations with micro-dispensing technology
The basic principle of micro-dispensing is the utilization of a precision dispenser to apply small amounts of lubricant needed (less than 1 percent of the air-fluid mixture) to effectively perform the metal cutting operation. As a result, the lubricant is essentially consumed during machining. No residue is left on the machine or workpiece, nor is there any airborne mist.
Technological Developments
Advances in nozzle designs have improved lubricating performance substantially by increasing the velocity of the lubricant carrying airstream. This allows a high-velocity airstream to be directed at the tool/workpiece interface while minimizing the tearing effect—the propensity to form droplets—in the lubricant.
Older designs induce rapid decompression at the nozzle tip, which reduces velocity dramatically as the air-lubricant mixture is delivered. This creates a tearing of the lubricant into droplets with very little mass, thereby reducing the droplets’ striking power. Additionally, since a droplet’s mass is lighter than air, the result is more like fog than a well-directed stream.
Tests performed on earlier nozzles illustrate a severe reduction of lubricant being delivered to the workpiece at distances greater than three inches. And less than 30 percent of the lubricant actually made it to the test surface at a distance of 6″ from the nozzle. This means that 70 percent of the lubricant either remained suspended in the air as a fog or settled onto machine surfaces and the shop’s floor—everywhere except where it was needed.
Newer nozzles deliver 90 percent of the lubricant to the same test surface. The improved design utilizes laminar airflow along the outside of the nozzle. The lubricant and air are carried in their own separate, dedicated lines. The lubricant, which travels inside the nozzle tip, is introduced into the air stream outside and in front of the tip. This external laminar flow eliminates the rapid decompression of the air-lubricant mixture. With the new design, droplet mass increases to a point where excess lubricant does not remain airborne as fog since the resulting droplet mass is heavier than air.
Applications
Tapping is one operation where micro-dispensing, combined with the proper lubricant, excels. In one application, a vegetable-based lubricant reduced the number of 12-28 nitride taps required for tapping 304 stainless steel castings. Before switching to the vegetable-based lubricant, each hole required a two-step tapping procedure and tool life was 35,000 to 40,000 individual operations per tap. After switching lubricants, each hole required only a single tapping procedure and tool life increased to 55,000 to 65,000 holes per tap. The improvement resulted in a 25 to 33 percent reduction in process time for the job. Also, since cleanup was eliminated, additional savings were gained prior to plating the finished parts.
Milling is also a good fit for micro-dispensing. The high-velocity air ensures excellent chip clearance and lubricant application. Both feed and speed rates can be increased significantly without reducing tool life.
Delivering coolant or cutting oil by traditional spray methods is less cost-effective than micro-dispensing. A direct comparison was performed for a milling operation by first spraying coolant and then switching to micro-dispensing. Spraying required over 2 gallons of coolant while micro-dispensing required less than 2 ounces to do the same job. When such small amounts of lubricant are delivered to the cutting zone, there is no airborne mist or residue produced—and operator safety is enhanced.
Turning most metals is also greatly enhanced with micro-dispensing. Reduced tool wear is an immediate result.
In an application that involved turning a nylon part, heat reduction was critical to prevent the workpiece from melting. Flood coolant allowed the speed to be increased, but the nylon continued to melt. Micro-dispensed fluids, however, prevented heat buildup, allowing the nylon chips to remain brittle and break. Micro-dispensing also improved part finish and permitted a 20 percent increase in speed and a 10 percent boost in the feed.
Micro-dispensing can make drilling more efficient, too, since the high-velocity air carries the lubricants into the hole more effectively. Reduced cycle times, longer tool life, reduced chip welding and improved finishes have been realized.
Band sawing is yet another operation that benefits from micro-dispensing technology. By precisely directing the nozzles at the blade, it remains clean and effectively lubricated.
Micro-dispensing with advanced fluids has proven effective when sawing structural shapes up to 6″. Interrupted cutting is also enhanced because the lubricant remains on the bandsaw blade between cuts.
Operational Savings
Besides saving on fluid costs,micro-dispensing can be a profit center. Producing dry chips increases their scrap value. And since micro-dispensed lubricants make up less than 1 percent of the air-lubricant mixture, post machining lubricant residue on chips is practically nonexistent.
Moreover, micro-dispensed parts that require heat treating, plating, painting, or anodizing no longer require intensive cleaning after machining. Additionally, part-cleaning solutions last longer, finishing costs are reduced, and machine surfaces, shop floors and tools are cleaner.
micro-dispensing is an alternative to flood and spray cooling for many applications, but each method has its place. When all three methods are available, a shop’s lubricating and cooling arsenal is complete.
Need more information on Micro-dispensing
Contact us, we will be happy to help you with the appropriate system for your application.
- Category:
- Application
- Tags:
- Metal Cutting