Advancements in Constant Level Oilers
Adapting to innovation in the lubrication sector can often feel like a slow process. It's intriguing to consider why many organizations hesitate to embrace new technologies, particularly when these advancements offer cost-effective enhancements that significantly improve lubricant protection for equipment. The reluctance could stem from a fear of change, the perceived hassle of undergoing procedural updates, or simply a lack of awareness about these innovations, leading to satisfaction with current setups. This article will delve into the evolution of constant-level lubrication systems, highlighting key developments over time.
The Vented Opto-Matic – A Solid Foundation
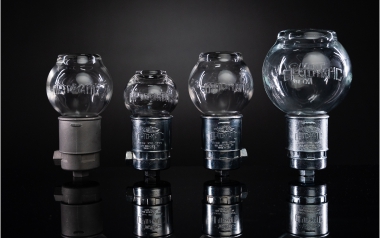
First introduced in 1939, the
Opto-Matic® Oiler set a new benchmark for industries throughout North America and later, the globe. After its US Patent expired, numerous imitators emerged, offering similar products without any genuine innovation in functionality or design. The Opto-Matic's primary objective is to maintain a constant lubricant level within machinery, relying on an additional lubricant reserve in the supply reservoir. The function is straightforward: as oil levels drop due to consumption or leakage, air enters the reservoir, prompting oil to replenish the system until the desired level is restored or the reservoir is depleted. This oiler also became an industry specification in the API 610 standard forty-plus years ago. This system serves as an effective method for maintaining optimal lubrication levels.
The Closed System Opto-Matic – An Enhanced Solution
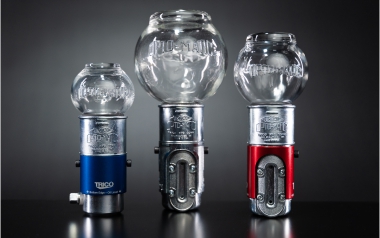
The 1990s saw the introduction of the
Closed System Oiler, or closed-loop oiler, representing a significant improvement over the vented Opto-Matic model. The original vented design, which draws air from the environment, posed potential risks for contaminant entry. The closed system addresses this by sealing the reservoir with an O-ring, thereby blocking potential contaminants. It requires an air source but connects to the bearing housing via a pressure balance line, creating a closed-loop environment that also prevents oil leakage (from pressure inside the bearing housing) or unintended intake into the bearing housing (from a vacuum condition). This model features a sight glass for direct level setting and monitoring, complies with the API 610 standard including a wire guard, and introduces "positive stop" level adjustment screws (identified by the red collar) for precision. It's designed for easy installation in place of the vented model, offering substantial contamination control improvements for a marginal cost increase.
Sensei Enabled Closed System Oiler – The Pinnacle of Innovation
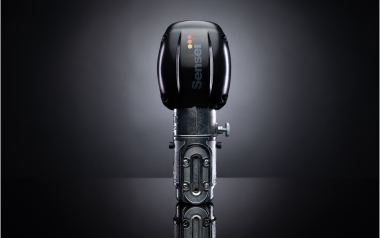
In 2018, the lubrication field was further revolutionized with the introduction of the
Sensei platform, making the Vented and Closed System Oilers the inaugural "Sensei Enabled" products. These devices now have the capability to transmit real-time data to the cloud, accessible from any electronic device, anywhere, anytime. Imagine the efficiency of monitoring oil levels in numerous reservoirs simultaneously from a computer, swiftly pinpointing which systems need attention. This technology enables users to track historical data, identify frequently problematic equipment, and calculate oil consumption accurately. Integrating traditional lubrication methods with cutting-edge technology, the Sensei platform represents a significant leap forward for the lubrication industry, and constant-level oilers, with more innovations expected as the platform evolves.
Consider the potential benefits of upgrading your lubrication systems to the latest technology next time you're in the market for constant-level oilers. Embracing these advancements, whether functional or technological, will elevate your lubrication program to new heights, regardless of your current practices.