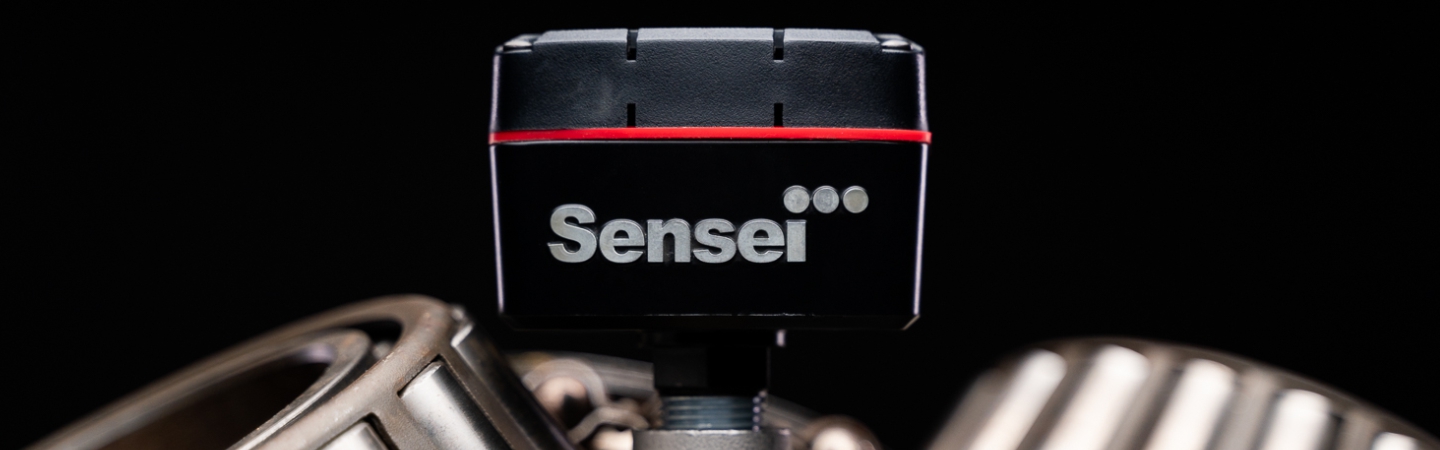
Dan Freeland
04.02.2024
Conrtrol your unplanned downtime. Control the outcome.
What if you could look at live data from all of your equipment that encompasses many of the parameters that are used in equipment inspections, and not coincidently, are the same parameters that are prevalent in machine failures?
For many assets that are starting to or are having issues, there are certain commonalities. It doesn’t matter if the viscosity has changed, additives have depleted, particle contaminants, water contamination, misalignment, seal failure, mounting issues, cavitation, or bearing issues, they all create heat, vibration, noise, and/or pressure. These, along with humidity, are the exact parameters that, if unchecked, can mount up and in the end, create the dreaded unplanned events that cripple maintenance teams.
Implementing online sensing equipment like Machine VitalsTM to monitor and analyze the internal and external temperature, pressure, and humidity, along with acoustic and acceleratory variances of bearing housings, gearboxes, and hydraulic systems among others, can offer a wealth of insights and benefits.
Early Fault Detection is THE KEY
Temperature Trends: By comparing internal and external temperatures, you can identify abnormal heat generation within the equipment, a common early warning sign of issues like bearing failure, inadequate lubrication, or misalignment. An unusual increase in internal temperature relative to the external environment could indicate frictional heat buildup, which precedes many types of mechanical failures.
Pressure Patterns: Variations in pressure within a system can indicate several issues, such as leaks, blockages, or filter clogs, especially in hydraulic systems. Monitoring pressure trends can help predict seal failures or the need for filter replacements before catastrophic failures occur.
Humidity Levels: Monitoring humidity inside equipment like gearboxes and comparing it with external conditions helps in detecting water ingress, which can lead to corrosion, lubricant degradation, and premature failure. This is especially useful in environments with high humidity or those prone to condensation.
Acoustic and Acceleratory Variance Trending: By correlating temperature changes with acoustic and vibration data, Machine Vitals can help assess the quality and efficacy of lubrication within the system. For instance, an increase in temperature alongside elevated noise or vibration levels might suggest that the lubrication is failing to reduce friction effectively, indicating it may be contaminated, degraded, or insufficient in quantity.
Each of these parameters and/or a combination of them can alert personnel of unfavorable trending or when limits are exceeded providing an early warning that something just isn’t right with that asset.
Predictive Maintenance Scheduling
P-F Curve Utilization: The P-F (Potential Failure to Functional Failure) curve is essential for predictive maintenance. By monitoring the mentioned parameters, Machine Vitals can help identify the initial point of failure (P) and estimate the time until functional failure (F), enabling maintenance to be scheduled before the failure leads to downtime, thus optimizing maintenance schedules and extending equipment life.
Operational Efficiency / Optimized Performance: Continuous monitoring allows for adjusting operational parameters to maintain optimal conditions, reducing energy consumption and wear. For example, identifying and correcting misalignments can reduce energy consumption and wear on bearings and gears.
Data-Driven Decisions with Cloud Aggregation and Analysis: With data collected by Machine Vitals, cloud-based algorithms can perform trend analysis, anomaly detection, and predictive analytics. This analysis can inform decisions on maintenance strategies, equipment redesign, or replacements, and improve overall system design and reliability.’
Implementation Considerations
To leverage these benefits, Machine Vitals sensors should be configured as follows:
Temperature, Pressure, and Humidity Sensors: Continuous monitoring for both internal and external sensors allows for real-time comparison and trend analysis.
Acoustic and Acceleration Sensors: Focus on identifying patterns and anomalies that indicate mechanical issues or failures.
Assigning Limits: Assign the limits of expectations for each sensor to alert when the sensors pass over a threshold that can be fine-tuned over time.
Maintenance event tracking: Include all maintenance events for each asset in the Sensei software by using the mobile app so you can also see what was done, when it was done, and the resulting equipment ramifications of the event. This maintenance history can also be very useful when performing post-momentum analysis, along with the historical sensor data.
By integrating these early detection insights into maintenance and operational strategies, organizations can significantly improve equipment reliability, reduce downtime, and optimize performance, leading to substantial cost savings and enhanced operational efficiency.